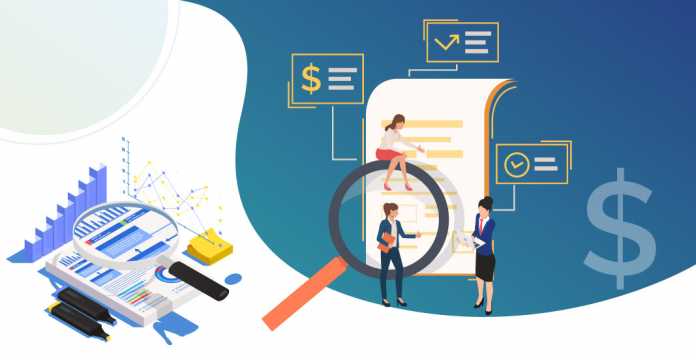
Quality Management tools are effective methods of streamlining business activities. While the goal is always to produce better quality and faster results, the cost to the company cannot exceed the benefits. In this article, let us focus on the Zero Defects approach in Quality Management.
Out of a sample of 600 companies, 91% saw an increase in operating income after the implementation of a quality management tool. Tackling quality is, in theory, one of the quickest ways to increase returns on production. Businesses can handle this through innovation and streamlining processes and overheads. The “Zero Defects” method works to reduce quality defects to non-existent and as a result, create better value for time spent.
Introduction to Zero Defects
In 1979, Philip Crosby (businessman and author) wrote the book “Quality is Free”, where he coined the term “zero defects”. He detailed that when zero defects occur in the production processes the output created is precise therefore no costs are associated with creating the intended quality and as a result “Quality becomes Free”.
Zero defects explain the production process that contains no flaws and works seamlessly from start to finish. With this concept, no extra materials are utilized within the production process and as a result, lack of failure increases profits and in turn, revenues could increase the development of customer satisfaction.
The process itself contains no rules or step-by-step guide. “Zero Defects” acts as a philosophy or mentality to apply when conducting business activities. The adaptability of this concept allows for any business looking to streamline activities to introduce the policies needed to execute the same.
Zero defects at its core represent the idea of defects per million opportunities or DPMO; it is defined as 3.4 defects only per million opportunities.
How to Achieve Zero Defects?
In order to introduce “Zero Defects” into an organization, an internal assessment of the business process needs to be conducted by asking the following questions:
- Does the organization recognize the high cost of quality issues?
- Does the organization constantly identify where prospective issues may arise?
- Does the organization work to proactively identify and address flaws within the production system or within business processes that allow defects to occur?
These questions are asked to establish a basis to build a strong foundation to execute the “Zero Defects” system. The management of the organization must be committed to creating a ripple effect from the highest levels within the company down to the cogs functioning on a granular level.
- In order to introduce the zero defects approach, principles of change management can be used to soft-land employees into the transition
- Clarifying customers’ expectations of quality will help create cognizance within the design process. Creating systems for product development and design that don’t incorporate extra elements or anything the end-user would be able to deduce does not add value
- The Zero defects approach requires companies to proactively approach business processes
- Introducing teams with an organization that focuses on improving quality needs to be implemented. The philosophy of zero defects must be incorporated into the organizational culture. The concept needs to rest at the core of all business activities instead of optional incorporation
- Introduce the Japanese system of “Poka-Yoke”, invented in the 1960s by Shigeo Shingo (a Japanese industrial engineer with success at Toyota). The phrase translates roughly to “preventing inadvertent mistakes”. The approach requires product designing systems to make defects almost impossible to create or if problems are unavoidable, easy to detect and rectify
- Keeping track of progress is critical to the success of “Zero Defects”. Introducing systems and mechanisms that allow for consistent feedback to build more streamlined systems allows business owners to jump into action when issues arise
- Understanding the efforts exercised within the quality control process is of paramount importance. Approaching the process from the base allows organizations to understand in entirety the cost of defects to the business and the benefits of ensuring they no longer exist
- Introducing the concept of quality into expectations regarding performance allows for members of the organization to understand how to inculcate zero defects into their day-to-day activities and understand the rewards that develop out of the same
- The zero defects concept is cyclical. Understanding that business processes are dynamic and the processes that affect these processes need to be flexible enough to adapt to the same is necessary. Therefore when implementing a zero defects approach, one must constantly monitor, evaluate, and adapt to a constantly developing cycle
Reasons Why Zero Defects is the Best Quality Management Tool
Zero Defects is a minimal investment quality management tool that allows for quick implementation of better business practices with results that are seen with minimal lag time. The process cuts down effort and cost elements associated with defects, overproduction, waiting, non-utilized talent, transport, inventory, motion, and extra processing. There is one hundred percent dedication towards streamlining the creation process internally. Any detectable issues need to be addressed but in preference, the methods themselves are tweaked and adjusted.
It is also equally important to understand the concept of an entirely zero-waste production process veers toward unrealistic. There may be instances where dedicated time and resources are not performing the way they should and as a result, the malleability of the “zero defects” process tends to shine.
The concept is flexible and adaptable to any organization, and in reality, any business entity could afford to work on quality management and build long-term benefits from the same.
Conclusion
The implementation of the “Zero Defects” philosophy offers companies the opportunity to understand and streamline their production process down to every minor detail. The minimal costing and maximum returns on implementation make it ideal for any organization looking to introduce a new business concept without training and recalibration investment.
With a 114% increase in stock performance of companies that incorporated a total quality management system, any company looking for positive development must at least consider introducing “Zero Defects”.
Final Thoughts
The Zero Defects philosophy is a powerful quality management concept. The concept explores business processes streamlined to contain no added elements or processes, just implement and execute approaches to create the highest quality goods and services. The flexible concept is adaptable to any business environment at minimal investment. Businesses that adopt the Zero Defects principle see improvement in customer satisfaction and business returns.
It is crucial for individuals and enterprise teams to get trained and certified in popular Six Sigma Certifications and Quality Management Courses to gain a proper understanding of the Zero Defects approach and how it can add value to an organization.
Some of the popular quality management certification courses that individuals and enterprise teams can take up are:
Lean Six Sigma Green Belt Certification
Lean Six Sigma Black Belt Certification Training