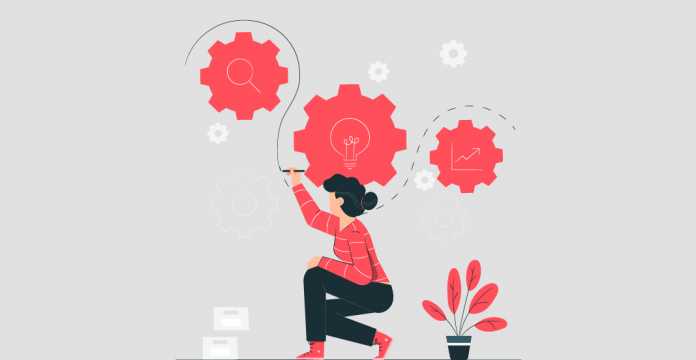
In today’s challenging business landscape, enterprises are struggling to meet complex market demands and deliver value to the consumer. It is in this regard, organizations are implementing the Six Sigma methodology to deliver real value and also achieve better ROI. In this article, let us explore what is value stream mapping.
What is Value Stream Mapping?
Value stream mapping is one of the key Lean Six Sigma tools/techniques used to provide a detailed visualization of processes in an organization. In layman’s terms, it clearly showcases the flow of goods from third-party vendors to customers through your organization. For the IT services industry, it is how software solutions are delivered to your customers with all features.
Lean manufacturing or business methodology is used to track, evaluate and optimize the flow of information or resources needed by a company to manufacture a product or service.
Value stream mapping (VSM) is a paper-and-pencil technique that lets you see and appreciate content and knowledge flow as a commodity or service flows across the stream of value. Value stream mapping is usually used in Lean, which varies in four ways from Six Sigma’s phase mapping:
- It collects and displays a much wider variety of details than a traditional process diagram.
- It appears to be higher in level than specific phase maps (5-10 boxes).
- It appears to be used to a more considerable degree, from receiving raw materials to providing finished products.
- It appears to be used to define where potential tasks, subprojects, and kaizen activities can be focused.
A value stream map (AKA end-to-end device map) takes into consideration not just the product’s operation but also the control and information processes that help the specific function. This is extremely useful when trying to minimize processing time since in addition to the process flow, you gain insight into the decision-making flow. Indeed, it is a Lean tool.
The simple principle is to map the process first, then map the information flow above it, which helps the process to take place.
Why Use Maps On Value Stream?
Visualization of essential data and knowledge within the VSM defines reasons for duplication and change in the process phases. For starters, if your emphasis is on that cycle time and waiting time is 90% of the overall cycle time, it would flag what you need to do. In comparison, if 80 percent of the waiting period is in two of the 18 stages of the procedure, you know where the key prospects are. VSMs may be used as required by the team for the current state process, the future state process, the whole process, or a section of the process.
How VSM is Practised in Various Departments?
- In manufacturing: Analyzing every step in material handling and information flow to identify waste in the production process. This is where lean methodology started at Toyota in the 1950s, and lean methods and value generation surveying remain key to the manufacturing industry. They have, of course, since distributed to other areas and become interwoven with Six Sigma methodologies and Lean Six Sigma methods.
- Supply chain and logistics: Identifying the root cause of waste and expensive delays at different points in the supply chain help to minimize product delays.
- Software engineering/development: To find software development shortfalls, from design to delivery, including feedback mechanisms and rework. While some critics question the value of VSM in a development approach, others find it helpful to gain efficiencies, like reducing waiting periods between stages or decreasing the need for revision.
- Service industries: Improving the value and finding waste in the operations needed to perform any service for external clients.
- Healthcare: Improving the measures taken to treat patients in its most reliable, safe, cost-effective, and high-quality manner.
- Office and administrative: finding wasteful steps and improving the service given to existing clients within a company.
Actions to Build a Value Stream Map
- Identify limits between procedure and method.
- Identify the process improvement focal point as described in the Project Charter.
- Identify the squad on quality enhancement.
- The team sketches the future state map of the operation, in the form of a flowchart or swim lane.
- Define the data/information necessary for focussing progress
- Data Selection
- Perform the Gemba (walk through the workplace): the most fitting data collection process.
- Most mechanisms (peak hours, seasons, etc.) differ over time.
- Using a collection and most likely importance when precise detail is not available
VSM Purpose and Benefits
Value stream mapping is a useful tool by which waste can be minimized in any operation, not just output. That is the primary aim. You explain each significant phase of the process and determine if it brings value from the customer’s point of view, or not add value. This value orientation keeps the research focused on what matters, helping the business to perform the most efficiently in the market. Lean practitioners may make effective use of VSM to generate the best value for the consumer in the most productive way possible, forestalling, or meeting any danger. Continuously it can and can be used for quality development, putting more and more procedure steps on site. VSM helps you not only to see the waste but also the source or origin of the trash.
As for most successful visualizations, the analysis of value sources acts as an essential method for connectivity, teamwork, and even cultural change. Decision-makers should picture precisely the actual state of the operation and where the excess occurs. They can see concerns such as production delays, unnecessary maintenance, limitations, and difficulties with inventories.
While its traditional aim is to reduce waste, VSM can also be viewed from the adding value viewpoint. This is what the consumer cares for, after all. Waste minimization is the path to end value formation, such as a lower price and a great or assistance that is of higher quality.
Conclusion
Effective implementation of Value Stream Mapping in an organization shows all process flow operations and highlights areas of inefficiencies and optimization opportunities. Including processing times, error frequencies, backlog, etc.
To gain an in-depth understanding of VSM, individuals and enterprise teams need to get trained in popular quality management certification courses to deliver actual value for the organization.
Some of the popular Quality Management training courses that professionals can take up are:
Six Sigma Green Belt Certification