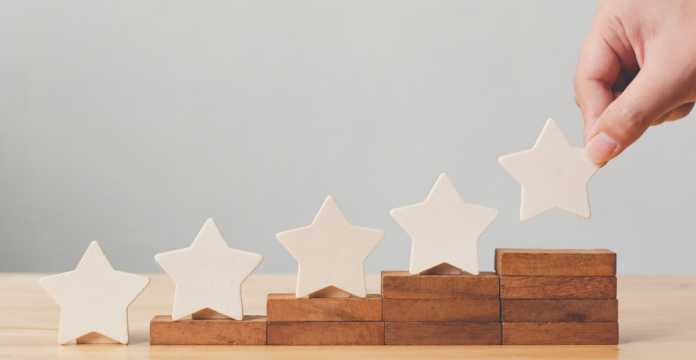
Total Quality Management is a technique that grew popular in the 1980s. It is an organizational culture that is focused on creating products to match consumer needs. It is focused on the high quality of the final results by improving the quality of all the processes and operations of a company. Total quality management eliminates defects and waste in the processes and focuses on doing it right from the first time.
The management and employees are both involved in total quality management practices and they both are responsible for the continuous improvement of production. This approach has multiple layers that involve tools to improve quality as well as management so that organizations can reduce their losses and generate more revenue.
Many of the biggest companies use total quality management practices in their production. Some of them include Motorola, Toyota Motor Company, Ford Motor Company, and many more.
What is Total Quality Management?
Total quality management can be defined as a management philosophy whose main purpose is the integration of all the functions in an organization so that they can focus on meeting the needs of their consumers and their business goals as a whole. These organizational functions include many departments such as:
- Marketing
- Finance
- Design
- Engineering
- Production
- Customer service
When it comes to philosophy, total quality management considers the entire company not as separate departments but as a collection of different processes. Total quality management focuses on improving these processes both collectively and separately continuously. It values the knowledge and expertise that all the employees bring with them to add to their plans and strategies. Simply put, TQM is focused on doing things right from the first time.
Originally, total quality management was applied to processes only in the manufacturing industry, but due to its flexibility and adaptability, TQM has slowly begun to be recognized as a general management tool that can be applied in any industry. A seven-year-long study measuring the success rate and effectiveness of Total Quality Management noted that the participating organizations observed over a 91% increase in their operating income. This is because TQM comes with incremental gains and not radical ones.
Total Quality Management has been manipulated and adapted in many industries by making some variations to the original methodology. The philosophy has given birth to many processes and activities in an organization such as:
- Commitment to meeting customer requirements
- Demand flow manufacturing
- Improvement teams
- Involving both senior management as well as employees
- Reducing the cost of the product or service
- Creating systems to help facilitate continuous improvement
- Empowering all employees
- Focusing on improvement plans for processes
- Creating ownership for line management
- Reducing the time for development
The practices mentioned above show that total quality management should encompass all departments in a company by all employees to achieve higher efficiency.
Principles of Total Quality Management
There are some key principles involved in total quality management which include management commitment, control of statistical processes, continuous improvement of all processes, and more. The main principles of TQM are listed below.
- Commitment from management teams
- PDCA form of implementation for process improvement
- Empowering all employees
- Training management and employees in TQM practices
- Creating a suggestion scheme to involve all the teams
- Measurement and recognition of processes and their success
- Decision-making based on facts
- Statistical Process Control using DOE and FMEA, and by using the 7 statistical tools
- Focusing on continuous improvement of processes
- Creating cross-functional processes
- Attaining set standards, maintaining and improving them
- Focusing on customer needs and requirements
- Creating and upholding standards set by the customer
- Creating a partnership with suppliers
- Maintaining and never compromising on the quality of the products
TQM and Concept of Continuous Improvement
A study conducted by GAO surveyed many private companies in the US that had adopted total quality management and observed that annually, on average, these companies accomplished the following after implementing TQM:
- 11.6% drop in complaints by the customers
- 12% reduction in order-processing
- 10.3% drop in the number of defects in the product
- 16.6% rise in employee suggestions
- 13.7% increase in overall market shares
These results show that total quality management is a continuously improving and evolving structure that companies can use to achieve incremental results. It includes all members of an organization, starting from the top management employees who handle strategic planning and decision-making as well as executives who work in the production line.
Total quality management not only focuses on improving the processes and results within a company but also on improving the capabilities of the people and machines for better results in the future.
TQM focuses on five areas that are involved in improving capabilities within an organization. These are:
- Demand generation
- Supply generation
- Technology
- Operations
- Employees
The main principle of total quality management is that although mistakes are often made by people, they could be the result of, or be permitted by pre-existing systems and processes that are faulty. This means that by finding the root cause of these mistakes and eliminating it, these mistakes can be avoided altogether.
Implementation of Total Quality Management
The PDCA plan is the most widely used form of implementation of total quality management. The four-step plan takes observing defects into account and working on different methods to eliminate them. It is a waste-elimination tactic used by companies to improve the quality of their processes, thereby improving the quality of their product.
Plan
The first phase of planning is where all the management employees along with executives work together to find problems in daily operations that need to be addressed. These issues could hamper productivity and the employees work together to find the root cause of these problems.
Do
Once the problems and the root cause of these problems have been identified, the next phase involves coming up with solutions for these issues. The Do phase of the PDCA plan involves developing strategies and implementing possible solutions to see whether it works or not.
Check
The check phase is where employees see how well the implemented solution is working to address the root cause of a problem.
Act
The fourth and final phase of the PDCA plan is the presentation phase. The results of the solution implemented in the Do phase of the plan are documented and presented to the teams to measure its success.
Final Thoughts
Total quality management as a methodology is focused on incremental gains when it comes to success by continuously improving the existing processes within a company and removing all possible errors. It helps organizations meet customers’ as well as stakeholders needs and expectations. TQM focuses on getting it right from the very first step itself so that there are no problems later on.
The total quality of an organization can be managed and becomes possible when employees and teams are trained in the methodology and mindset of TQM. Without developing a TQM-oriented work culture, the implementation process of TQM strategies will not be as successful.
Some of the popular Quality Management Certification courses that employees and teams can get trained in are: