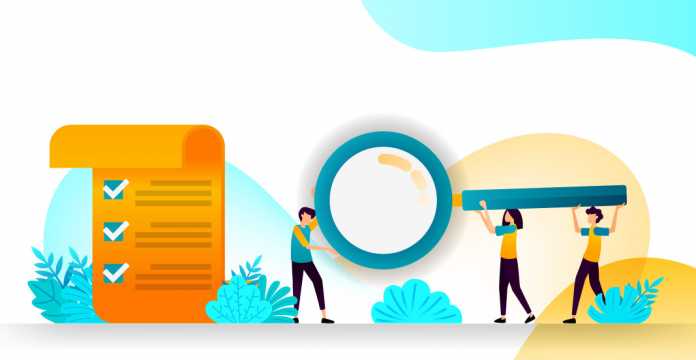
Poka-yoke (noticeable POH KA YOKE) is an error-proofing technique developed by the Japanese engineer Shigeo Shingo during the 1960s to remove errors or avoid errors. The term “poka-yoke” is derived from the Japanese expression “to prevent mistakes” Poka-yoke allows the use of straightforward but efficient methods and signs to avoid mistakes.
A basic example of poka yokes is to press your car keys to something you would like to take to work. It is clear. It is effective. That is what it wants. Don’t waste money on investments where a quick idea will work.
The Five Steps of Poka-Yoke
A Poka-Yoke consists of five stages:
- Describe the defect
- What is it that causes the defect? Go and behold, go to the Gemba. Gemba means the floor of work. This is where the mechanism takes place, and where the root causes of the defect can be found
- Analyze the phase the defect is observed in
- What is the reasoning behind the defect? Go, and check the root cause
- Develop a solution and get Poka-Yoke introduced
- Make sure the defect won’t be possible again in the long term
Applying Poka-Yoke
The HBR study says that one of the most significant features of the Lean technique might be the no-frills of poka-yoke, a realistic solution to avoiding errors or identifying them instantly.
Mistakes cost money in sales, which hurts the bottom line. The levels are higher in other occupations. A health care provider, for example, who makes a minor mistake (wrong drug, missing suture during surgery) may cause serious health emergencies.
Even if the errors do not seem instantly serious, it is necessary to have poka-yoke. As noted in the HBR post, nothing compromises honesty as though it were a readily avoidable error – think about Excel miscalculation, a misspelling about PowerPoint, or a lost email. Such minor mistakes may affect business relations, damage customer loyalty, or cost a company.
Learning Poka-Yoke
Lean and Six Sigma’s attention is on finding and disposing of waste and defects. Poka-yoke plays an integral part in this region. The awarding of a Six Sigma belt and credential is a wise first step for professionals who want to take on a leading role in developing company operations.
Common Poka-Yoke Tools
- Various Lean tools are used in Poka-Yoke: Method mapping: A graphic description of the operational phase
- Five Whys: by questioning why you get closer to the root cause of a problem five times, and finally, the solution
- Go to the Gemba: go to the work floor this is where the procedures occur, but the faults still occur
- Cause and Effect Diagram: A guide for dilemma analysis. Can be used to enhance industrial practices and quality control
- FMEA (Six Sigma Tool): Study of Ineffective Modes and Consequences. A framework that analyses a product or service framework configuration and detects potential errors. After that, the action is taken to eliminate or mitigate them
3 types of Poka-Yoke
Three forms of Poka-Yoke can be defined to provide solutions for development challenges quickly and easily.
Visual Aid
This help is evident and provides directions for the job. There may be pictograms indicating a limit or warning in a user manual or a street sign.
Visual Control
These apply to conduct direction and alarm in the event of deviations. For instance, if cars adhere to the speed limit, a traffic sign will light up red when cars are driving and green.
Fail-safes
They push the user to do something, yes, or not. E.g., this would be roadblocks for the repair of the motorways. Arrows on signs move drivers to go from lines 3 to 2 and 2 to 1. On the boards, the hands are accompanied by red Xs before 2 of the 3 lanes are closed.
Poka-Yoke Stumbling Blocks
There might be instances where you expend a lot of time and money on poka-yoke only to find it eventually discarded and stick to the original methods. This usually arises because the selected poka-yoke has the following pitfalls:
- In the duration of execution, it has become too demanding for the manufacturer
- It was so rigid it limited the system productivity
- It was unstable, causing some faults to slip through. These faults may have halted production too frequently
It’s crucial to ensure that poka yokes are effective, quickly controlled, and not burdensome if you want them to achieve their goal of increasing efficiency and reducing flaws. Another weakness is knowing individual boundaries when enforcing a poka-yoke. Examples may include:
- Vision
People have different abilities to discern specifics and colors.
- Hearing
The upper and lower levels of hearing of a person can differ, and may also alter by adding background noise.
- Performing repeated tasks
Mental monitoring and muscle performance are decreasing as repeat rates increase.
To learn more about this methodology and how you can benefit from it, individuals and enterprise teams need to get trained in popular Quality Management Certification courses.
Some of the popular Quality Management training courses that professionals can take up are:
Lean Six Sigma Green Belt Certification Training
Lean Six Sigma Black Belt Certification Training