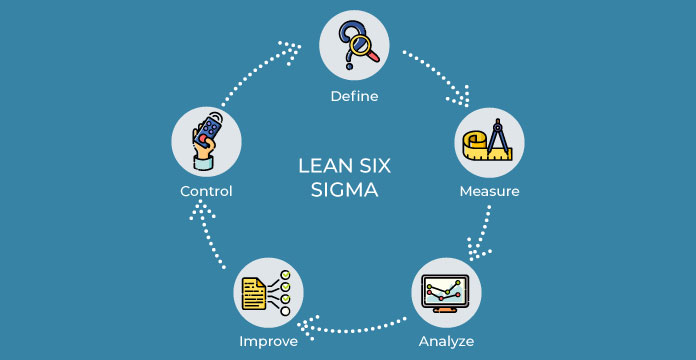
Manufacturers across the globe know the value of Lean and Six Sigma and what it brings to the table. These proven process improvement methodologies have helped many enterprises to improve their productivity, and ROI, increase the bottom line and improve the overall customer experience.

According to the latest research report, it indicates that 75% of organizations adopting Lean Six Sigma methodologies have reported significant financial benefits. But then many enterprises and businesses, in general, have not discovered the true value of Lean Six Sigma and its applications.
There are various reasons why enterprises do not implement Lean Six Sigma. Few of them are valid reasons and some of them are pure misconceptions.
Below mentioned are some of the top 10 reasons why organizations do not use Lean Six Sigma.
1. What is Lean Six Sigma? We’ve No Idea:
This, in today’s time, is difficult to understand that an enterprise has no idea about Lean Six Sigma, but we can still consider it a valid reason because Lean Six Sigma was extensively used in the manufacturing scene and had very less exposure outside. Successful pioneers like Henry Ford and Taichi Ohno were instrumental in implementing Lean Six Sigma for their respective manufacturing plants which helped them to save billions of dollars in revenue and achieve a greater ROI and increase their overall bottom line. You may as well start to read these success stories with Lean Six Sigma and initiate your organization’s journey to realize the benefits that it has to offer.
2 Lean Six Sigma has Failed to Take off Just Like TQM:
Let us not go into the debate of whether Lean Six Sigma failed as TQM (Total Quality Management). TQM had its own shortcomings as a process improvement methodology. Whereas Lean Six Sigma has a different approach and has a far better foundation than TQM. In the mid-late stages of the 19th century, business stalwarts like Edward Deming, Henry Ford, and others implemented Lean Six Sigma and availed immense benefits that it had to offer. Lean Six Sigma has survived all these years only due to its robust principles such as: sharply focusing on the customer; usage of data and analytics to make informed decisions; and the ROI language of management. It is for these reasons that Lean Six Sigma is still relevant in today’s service-based environment.
3. Lean Six Sigma can Only be Applied to a Large Organization:
There is a big misconception that Lean Six Sigma applies only to large enterprises. Even the smallest companies in the world which have less than 10 employees deploy Lean Six Sigma methodologies to improve processes and streamline their services. There is a growing complaint from many SMBs across the globe that they are not able to take their business to the next level even when they are profitable. Reasons such as their cash flow being tied up in inventory or receivables, unable to provide better customer service, employee productivity, etc can all hamper the growth. Lean Six Sigma and its DMAIC concept streamlines your processes and helps the business to be supple and cater to the demands of your customers and reach the level that you intended to.
4. We Cannot Accommodate Lean Six Sigma as a Dedicated Program:
We have heard this excuse a lot in our lives; we have no time for this and no time for that, then how come people achieve extraordinary results with the same 24 hours that we possess? It is just a lazy attitude or even worse they have been institutionalized where they want to do the same thing again and again and fear change. One of the valuable commodities for any organization is ‘Time’, waste it and you are losing something that cannot be replaced. It has to come from within the organization to change the attitude towards Lean Six Sigma and its holistic approach can solve a lot of problems that organizations are currently facing.
5. Implementing Lean Six Sigma Requires Ridiculous Costs:
Applying Lean Six Sigma does not require ridiculous investment. It can be started by only a few key personnel with their Yellow belt training and get started with the basic understanding of Lean Six Sigma in an enterprise. Then you can bring in consultants who are Lean Six Sigma Black Belt certified and start training your employees in the methodology. It is a one-time investment that will give you significant returns for a long period of time.
6. Fear of Change:
This is one of the most legitimate reasons why enterprises do not adopt the Lean Six Sigma methodology. This fear of change or the fear of the unknown has stopped individuals and enterprises to reach greatness. It is like their pride is at stake and they are too stubborn to implement something new. Though Lean Six Sigma is for an enterprise and its process, most of these processes are driven by people and ultimately it is they who have to consciously decide whether they have to implement Lean Six Sigma or not. This fear of the unknown prevents people to learn or develop new skills, taking up leadership roles, and implementing Lean Six Sigma. This fear should be driven out of the enterprise for them to be more creative and innovative to cater to the demands of new-age business demands.
7. Lean Six Sigma is Better Suited for Manufacturing Companies:
This has to be the biggest misconception of all, ‘we are not manufacturers to implement Lean Six Sigma – Lean Six Sigma has a universal application. Though Lean Six Sigma started its journey with manufacturing companies to reduce wastage, its applicability is more seen in service and transaction environments where there is a fair share of repeatable processes. There are many businesses that employ Lean Six Sigma outside the manufacturing sector such as AT&T, Wal-Mart, Starbucks, Merck, Coca-Cola, Bank of America, and more. Repeatable processes such as order processing, delivery, invoicing, accounts payable, employee onboarding, etc, with high volumes and data collected at each and every point, you have all the necessary ingredients to implement Lean Six Sigma principles to streamline these processes.
8. Lean Six Sigma is Just Statistics and Advanced Mathematics:
Most of the time enterprises shy away from Lean Six Sigma because of its statistics and advanced mathematics approach. But everything is not statistics and advanced mathematics in Lean Six Sigma. In fact, most organizations do not even require these to implement Lean Six Sigma. One can easily implement some of the basic principles and tools to start with. Wastage can be identified by having another set of eyes overlooking the processes and deriving a process map to do a gap analysis, and check for bottlenecks and redundancies.
9. We Just Need Lean and do away with Six Sigma:
This approach is not advised as Lean and Six Sigma go hand-in-hand where Lean principles improve the speed of your business output and Six Sigma improves the quality of your products and services. When you have the chance to get things right in your first attempt, why even consider an incremental approach of applying Lean first and then go for Six Sigma? You can increase both the effectiveness and efficiency in one attempt rather than sacrificing effectiveness for efficiency. In a similar manner, by implementing only Lean you are sacrificing quality and by implementing only Six Sigma you miss out on efficiency. Only when you combine both that you derive the maximum advantage that Lean Six Sigma has to offer.
10. Lean Six Sigma Deployment Failed Big Time:
Any implementation for that matter fails due to various reasons. As an enterprise, did you examine the reason why it did not work for you in the first place? Few questions you need to ask regarding why Lean Six Sigma did not work out:
-
- What was the primary reason for adopting Lean Six Sigma?
- Was there commitment shown by the senior management for the program?
- Was it related to people, processes, or technology?
- What were the metrics for success?
- Was your organization mature enough to handle Lean Six Sigma?
- Were employees equipped with the right training? There are many such questions that might give you the answer. First get to the root cause of why it did not work out, fix the problems, and then try again. You have to define the problems that you are trying to solve and then work with your employees and you can also ask your customers to be a part of the process. Also, Lean Six Sigma and its processes improvement methodologies are only as good as the people managing it.
Many enterprises across the globe have embraced the Lean Six Sigma methodology to improve processes and achieve excellence. So avoid procrastination about adopting Lean Six Sigma for your business by giving above mentioned reasons. Start your Lean Six Sigma journey and slowly start implementing the process improvement methodologies to take your business to the next level.