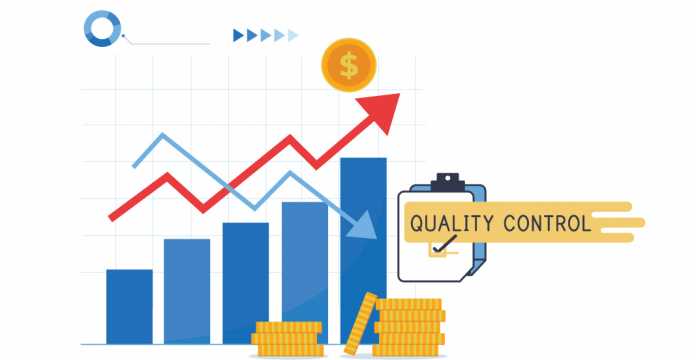
What is Minitab?
Minitab is software that was made to solve problems for organizations that use Six Sigma. Minitab gives working professionals an easy way where they can put all of their statistical data together as well as manipulate it so that the Six Sigma teams can identify upcoming trends and use them to solve existing problems. It is an extremely valuable and effective tool used by companies that use Lean thinking.
How Do Companies Use Minitab?
There are a lot of elements involved in Six Sigma that are incorporated in Minitab. Companies use Minitab to handle their data and statistics. Some of the tools offered by Minitab are listed below:
- Boxplots
- Scatterplots
- Histograms
- Descriptive statistics
Why do Six Sigma Professionals Need Minitab?
Most Six Sigma professionals have already been through training to give them the expertise to manage hard data, but still, most Fortune 100 companies (over 90%) use Minitab Statistical Software for their work.
So why is there a need to use the software when the working professionals are already trained in the principles of Six Sigma and their processes? The trained professionals are only trained in interpreting data. This does not mean they have the ability and skills to understand or realize the true root causes of any problems that the company’s processes might be facing. This makes the overall problem-solving and solution-finding process a lot faster and easier.
Using Minitab to Achieve Statistical Quality Control: A Case Study
Crayola is a globally recognized crayon-making company and they can be considered the leading company that makes crayons and art supplies for children. The only way that Crayola has reached and maintained this reputation is by ensuring all its products are of high quality. They need to maintain quality standards for all their products to remain a globally reputed corporation.
Now, something as simple as crayons may not be the thing people worry about when it comes to high quality, but to be the best at anything in the world, requires attention to detail and many strict measures to maintain the quality.
Crayola makes almost 3 billion crayons on a yearly basis, which makes it to almost 12 million crayons a day. This is a very high number of crayons for products that need to meet really strict quality standards. So, how do they do it?
Crayola’s Data-Driven Strategy for Maintaining their Quality
The only way a company as successful as Crayola can continue to operate and manufacture its products that keep improving upon its high quality is by maintaining a data-driven culture that is focused on continuous improvement.
Crayola uses Minitab Statistical Software to help them with their data analysis so they can improve their production line and processes. Minitab helps the company maintain a thorough statistical analysis of their data and shows them the trajectory.
Crayola implemented Six Sigma for their projects and managed to save over $1.5 million in 2008, and has not looked back since. Minitab has been in use for analyzing their statistical quality control and improving it from then onward with great success.
Practices That Help Maintain the Statistical Quality Control
Using Minitab alone is not going to smoothen and improve all the processes in the production and delivery of a high-quality product. Companies also need to partake in other practices to help maximize the potential for improvement of quality. Some of the practices companies can inculcate in their employees are listed below.
Get Full Commitment from the Entire Company
Everyone starting from the founder, the CEO, and the board of directors, to all the employees in the organization, needs to be committed to the continuous improvement philosophy. This is the only way all projects will stay on track and succeed regularly and religiously over time.
The entire company needs to be involved in making their projects successful. It is not just one team’s responsibility. All the employees need to be involved from the project approval until the delivery of the project. There need to be regular reviews of the progress as well as the implementation of improvements throughout the life cycle of the project.
This also acts as a motivating factor for the teams to work harder. Knowing that the board of directors is as involved in the making of a product as they motivate the team members to strive to achieve their goals with each project they undertake. All the ideas and suggestions need to be backed by data-driven strategies for creating a strong foundation for the entire company that embraces continuous improvement and change.
Encourage Creating an Environment that Supports Change and Growth
Organizations need to support their employees and encourage them to come up with new and innovative ideas for their projects. They need to create a platform for employees where they can feel free to bring new ideas to the horizon. They can use Minitab to compare these ideas and create predictions for more statistical and accurate analysis. The shared goal for the entire company is to achieve optimal delivery of products of the highest quality, and this open and communicative platform will help reach this goal.
Focus on Finding Root Causes and Creating Solutions
The accurate data analysis by Six Sigma professionals is of no use if it cannot be used to solve problems. The only way to handle all the defects or issues and deal with them permanently is to find the root cause of the issue and eliminate that.
Proper interpretation of accurate data analysis using Minitab will help in removing the excessive hard work of finding the root cause of a problem. This helps team members focus on fixing any issues that come up to enhance the continuous improvement process. Therefore, companies need a powerful tool to find root problems along with a disciplined team to solve them for a successful project.
Sustaining the Improvements
There can be a hundred new ideas and solutions to all the problems that get implemented, but unless these changes and improvements are sustained over a long period of time, they will be rendered useless.
Minitab acts as a standardizing tool that helps level all the improvements made so that the products can meet the quality standards of the company. Consistently improving while maintaining quality is important if companies want to achieve the success they are striving for.
Final Thoughts
A powerful tool like Minitab can really help Six Sigma teams achieve and sustain statistical quality control throughout their processes in the production and delivery of each project. Proper training in Six Sigma and other popular quality management certification training programs can help organizations utilize a tool like Minitab to its full benefit.
Some of the popular Quality Management training courses that professionals can take up are: