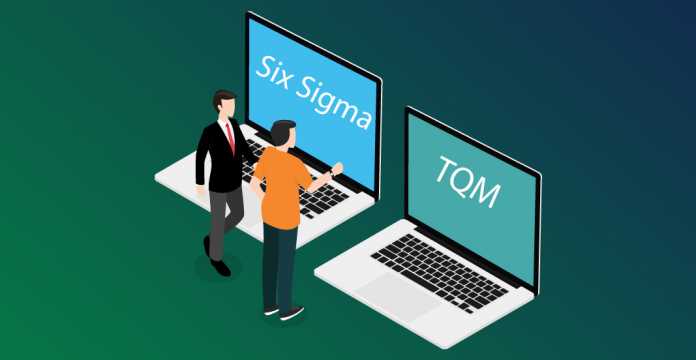
One of the crucial factors that govern the success of a business entity is the quality of its products and services. Therefore, companies are always on the lookout to find the best possible solutions for their quality management needs. While there are various frameworks and methodologies that have evolved over the years, most companies find themselves torn between two choices: Six Sigma and Total Quality Management (TQM).
Six Sigma is a data-driven methodology, which purely works on the statistical data retrieved from a research source. It aims to reduce the number of errors in a process by 3.4 or fewer defects per million items produced. Six Sigma helps enterprises to cumulatively increase profits in the long run.
The total Quality Management technique lays down a set of rules that are aimed to strategically improve the overall processes of a business. This, in turn, aids in building a high-quality product that customers accept and appreciate.
Six Sigma and TQM both are basically effective tools for quality management. While they have similar goals and may seem to be alike, there lies a meager line that sets them apart.
This article discusses how these two techniques differ from each other and in which aspects are they similar.
History of Six Sigma and TQM
The history of TQM dates back to the time when Joseph Juran used management tools such as statistical analysis and quality control, developed by Walter Shewhart, during his tenure with Western Electric Company. These methods were eventually developed solely for quality control by W. Edwards Deming in the 1950s which came to be known as TQM.
Six Sigma came into the picture at a time when TQM was already popular among companies as a tool for their quality management needs.
While TQM helped many companies grow, there were a few areas where it lagged. For example, focussing only on the quality, sometimes lead to overlooking other departments such as finances.
Six Sigma solved most of its issues, by delivering a more defect-focussed methodology that aimed at continuous improvement and eliminated the vagueness of TQM.
In 1987, William Bill Smith developed and implemented Six Sigma as a statistical approach to diminish errors from Motorola’s business process and products. Even though it was successful in improving the product quality at Motorola, this method failed to garner the limelight. It was only in 1995 when Jack Welsh adapted this technique at General Motors.
Quality Perspective of TQM and Six Sigma
“Quality” is a subjective term. One of the ways TQM and Six Sigma differ is how they both define “quality.” TQM defines “Quality” as a measure of how well a product’s features are manufactured by a company that meets its customer requirements. Here a “good quality “product refers to a product that is in alignment with the customer demands. Likewise, a “bad quality” product refers to something which the customer won’t be interested in investing in.
Six Sigma, on the other hand, defines “quality” as the measure of the number of defects a product or service may have. Since Six Sigma believes that error-free services and minimum defects in products grab more customer satisfaction, the term “good quality” refers to something with the least possible (or no) defect.
The Ultimate Goal of Six Sigma and TQM
Six Sigma and TQM have the same ultimate goal: Customer satisfaction. The methodologies to attain the same is what makes them different.
They share some common working objectives as well, which act as fuel to the whole process to attain their ultimate goal.
Both Six Sigma and TQM have the following goals in common:
- Production of high-quality services
- Monitoring of overall quality of the end product or service
- Keep the number of defects in the process and the product to a minimum
- Understand the area of defect and subsequent rectification
- Keeping employees in a happy and satisfying workplace.
Six Sigma v/s TQM: Approach and Focus
The approach to achieving the goals mentioned above is what makes Six Sigma different from TQM.
The primary focus of the TQM technique is to improve the functional aspect of each department in an organization, in a way that produces a high-quality product, which satisfies its customers to the highest possible extent.
The TQM approach fosters an amicable working culture where maximum involvement is solicited. It is primarily based on the work ethics, trust, and integrity of the business entity. There’s no hard and fast mathematical approach to achieving the best TQM practices for a company.
Six Sigma is more deterministic and fosters a data-driven and statistical approach. The prime focus here is to identify the areas of defects and plan out ways to reduce them in a way that there is a continuous improvement of quality. It also makes sure that the errors, once fixed, are not repeated, as it could deter the quality of the result.
Scope of Six Sigma and TQM
For a company to successfully implement either Six Sigma or TQM, it is very important to know for what purpose the organization wants to implement it in the first place.
Six Sigma is an effective method for correcting an error in an existing system or product via the DMAIC approach. It is also effectively used by companies to produce a new product with minimum or no defects through t the DMADV approach. Both these approaches clearly define the desired output in their first stage of implementation and subsequently understand the problematic areas, and then rigorously find solutions for the same.
This makes Six Sigma a reliable and versatile tool for quality management.
TQM works best where the organization is willing to promote an inclusive work environment, where managers are more like mentors, and team members are equally encouraged to participate in decision-making processes. It requires the company to train its employees to be able to make sound decisions that benefit the company and is in alignment with the organizational goal.
Six Sigma v/s TQM: Required Skills
Six Sigma and TQM have different approaches, as already discussed. Therefore, the skills required for the effective implementation of these two are different as well.
Six Sigma involves decision-making based on numbers and statistics and, therefore, the managers need to be adept in their respective fields. Six Sigma requires the skills of well-trained professionals. For this purpose, the professionals need to get trained in some of the popular quality management training programs such as Lean Six Sigma Green Belt, Lean Six Sigma Yellow Belt, and Lean Six Sigma Black Belt.
TQM, on the other hand, relies mostly on the sound decision-making abilities of the employees, which they can acquire from continuous training sessions and personal experiences. Therefore, TQM does not require any certified professionals. It only requires a good manager with the right leadership quality and a team working towards the betterment of the company.
Conclusion
TQM and Six Sigma methods are both effective methods to achieve quality control and hence attain their ultimate goal of customer satisfaction. Therefore, the result of implementing these methods may come out to be similar. However, the way to reach them is different. To completely realize the true benefits of Six Sigma, TQM, and Lean, individuals and enterprises need to train their employees in some of the popular Six Sigma Certifications and Quality Management Courses. This way, the workforce will be knowledgeable in TQM and Six Sigma best practices and how the same can be applied to their day-to-day work and business-critical projects.
Some of the popular quality management certification courses that professionals can take up are:
Lean Six Sigma Green Belt Training
Lean Six Sigma Black Belt Training