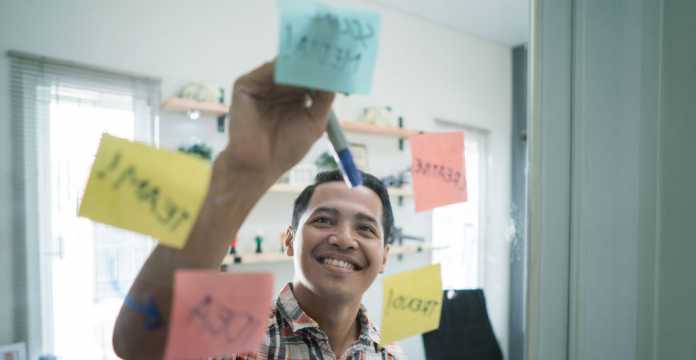
An essential feature of any Lean Six Sigma project is a process map – it helps explain the process at the heart of the project and directs you to unique target areas. There are a variety of choices available, and picking the correct map helps to make your efforts easier. In this article, let us explore more about the Six Sigma Process Map.

What is a Process Map?
Six Sigma process maps are usually created by the project leader, usually, a qualified Black Belt professional, but can also be delegated as a training activity to a team member. Using specialized flowchart software, which is incredibly helpful for more complicated mapping experiments, process maps can be created. Process maps can, however, be constructed using methods that are readily available in office suite applications, or can be drawn freely as well. The exciting thing isn’t how the map was made, but the precision of the mapping operation.
Several different types of process maps are used during a Six Sigma project. Phase maps that are most widely used include:
- Process Flow Chart – Simulation of a real workflow you strive to develop
- SIPOC Map – A diagram that shows sources, inputs, procedures, outputs, and clients for the product that you are dealing with.
- Swim Lane Map – Used to go further into an incident or operation and diagram all of a process’s subprocesses, hand-offs, and accountable pieces.
The Determination of a Six Sigma Process Map
Operating with a Lean Six Sigma development team consisting of five, eleven, twenty, or more would possibly provide each member with a clearer understanding of how a system functions and what could be changed. A system diagram has the aim of working together to produce a standard vision of the mechanism and how it can run. This exercise has several advantages like:
- Identification of process measures that add uncertainty and need simplicity
- Physically, compared to the present system with the planned potential model
- Making an interpretation of the process simpler for those not in the project team
Process diagrams are effective in any setting where Six Sigma methods may be applied, from clinics to bars and restaurants to plant production. Besides, Six Sigma method maps may be implemented to maximize outcomes at the start of a project or in the center of a continuing period.
Value Stream Mapping
A diagram of the value chain is generated to describe all processes engaged in producing the commodity from beginning to end. This value stream may include manufacturers, manufacturing processes, and end-users. Usually, VSMs concentrate on the flow of materials and details. Value source analysis for product production involves the design flow from idea to delivery. This is the broad way, staring at the entire arrangement for growth possibilities.
Stream Manager
A product family’s value stream can cross departmental borders within the business. This provides the opportunity for problems in managing productive project value sources. Such issues call for a value-stream boss to establish a new role. This boss must have the power to make it work, and report to the boss of the factory.
A production individual is assigned to do the role of value stream manager. That boss will supervise all facets of the project. The manager should continuously be on the field, being a hands-on guy.
Stream Mapping
Flow charts, workflow diagrams, written protocols, and job orders are tools used to evaluate and record the operations. Other Lean methods, like the visualization of value sources and spaghetti diagrams, are often used.
Building a Six Sigma Process Map
Keep in mind when making a process diagram that the map will appear like a flowchart displaying the phase start, the middle phases, and the conclusion — or planned consequence — of the method. For each key function that includes sub-steps, the chart might be a high-level overview or a far more comprehensive roadmap.
Assess Process Limits
Using an intensive care unit as an example will contribute to reducing waiting times for cases. The opening point of this case would be when the victim has come and taken out his paperwork, and when the patient is released will be the end.
List All Procedural Measures
The protocols would entail accepting the patient in our concept of an emergency room, having them sign up the referral papers, entering the specifics into the system, and allowing the patient to meet the nurse. Enter the inputs and outputs that are connected with each phase — the obtained articles or data (input) and anything that can occur from that phase (output).
Set the Steps in Sequence
Be assured to plan the measures in order to make it easy to find places for progress on how the new procedure functions.
Using the Symbols Correctly
Many Six Sigma system maps have the same group of characters, and each character reflects a distinct occurrence or point. Paint these symbols over each level of the process, and ensure that the whole team understands the meaning of every symbol. The most identifiable characters and ideals are:
- Terminator: The phase continues, then everything ends
- Rectangle: An action or task to perform as part of the protocol
- Oval: step inputs and outputs, or the whole phrase
- D: The “D” mark shows phase delays
- Arrow: Phase acceleration-an example of when the stream is increasingly flowing
- Diamond: A scenario in the system where you have to make a decision.
Verify Your Work
Evaluate the chart to ensure that it correctly describes and distinguishes each step of the current system. Have anyone beyond the project team — but still interested in the process — analyze the chart from their point of view and make sure nothing is missed?
Most projects utilize maps of various styles. You might start with a SIPOC, then a Map of the High Level. After any research, you will decide how to create a detailed chart of the particular parts of the regions where there are difficulties. After the discovery of root causes and the implementation of a new process, the Swimlane Map can provide valuable information.
To learn more about the Lean Six Sigma methodology, we recommend pursuing popular Quality Management certification courses, wherein you will get the opportunity to learn about all the concepts and techniques to make the most of this methodology.
Some of the popular quality management certification courses that individuals and enterprise teams can take up are: