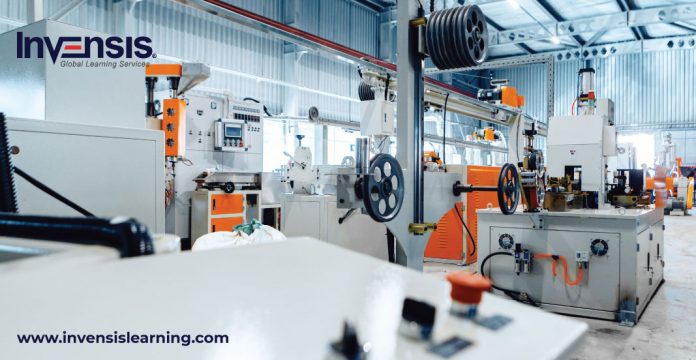
Six Sigma is a technique used to reduce the number of defects or errors in manufacturing. Implementing Six Sigma is to increase the quality of the products manufactured. The manufacturing industry has changed over the years with advancements in technology. Understanding the process and working towards quality improvement is the primary idea behind Six Sigma. Lean manufacturing is an additional concept that works in tandem with Six Sigma to decrease waste in the manufacturing process. So, this blog on “Six Sigma in Manufacturing | Advantages & Disadvantages” will discuss Six Sigma and its advantages and disadvantages in manufacturing.
In today’s competitive marketplace, quality is a crucial and distinguishing attribute in products and services. Lean Six sigma green belt certification is one of the most popular certifications among lean six sigma certification. The LSSBB certification is ideal for quality management professionals who want to keep their careers on the fast track and those who are leading projects for business improvement.
What is Six Sigma?
Every business has its problems while working on its operations. Resolving the issues in the business to increase productivity and revenue is the top priority of the organizations. Six Sigma or 6? is the technique or management approach used to improve business processes. It’s a standard method for developing strategies to improve business processes in the manufacturing industry. In addition, it mainly concerns quality, where faults or defects in the organization found to enhance the business. Therefore, reducing errors or defects is the primary objective of implementing Six Sigma processes.
Companies can increase the revenue or profits of the businesses with increased quality by reducing the faults in the products. In addition, it has various other benefits like cost-cutting, customer satisfaction, increased quality of the products, etc. The methodology has five data-driven stages: Define, Measure, Analyze, Improve, and Control. Before implementing Six Sigma processes in a business, organizations should analyze the various benefits and limitations.
Now, let us discuss Six Sigma in the manufacturing process.
Six Sigma in Manufacturing
Six Sigma methodology is primarily developed for the manufacturing industry, where faults or defects are the main problems. In manufacturing, the outputs will not be 100% accurate. In the production of a particular number, certain tolerances are acceptable. The more this number, the more the loss occurred in the production. Six Sigma helps reduce this number by identifying the core defects in the production and suggesting ways to overcome them. In addition, it explains the defects as the exceptions from the customer requirements. Six Sigma combines with lean manufacturing to reduce waste and thus reduce the defects in the production. It is called Lean Six Sigma, where both waste reduction and defect reduction are attained with a single methodology.
Six Sigma is based on data collected from the manufacturing unit and market. It is a data-driven or measurement-based approach that deals with the number of defects per million. Defects decrease to 3.4 per million industrial goods using Six Sigma. The various advantages and disadvantages of implementing Six Sigma processes in manufacturing are discussed here.
Read the blog to understand how using six sigma in Aerospace industry is impacting the the business?
We will now discuss Six Sigma in Manufacturing | Advantages & Disadvantages. First, we shall talk about the advantages.
Advantages – Six Sigma in Manufacturing
1. Quality Control
It is all about quality that matters! In manufacturing, every manufactured product is for delivery in the market. Therefore, any failure or defect in the product is considered a waste, and the product will not go on sale. Six Sigma helps improve the quality of the product by identifying its defects in it. Once the defects are identified, they are removed to improve the quality of the product.
2. Reduction of Defects
Defects, errors, flaws, faults, and failures are all exceptions from the customer’s perspective. The reduction of defects has fallen to 3.4 per million products made. It helps fix the problem in earlier stages rather than failing at the final production stage. It helps in reducing the costs initially after identifying and fixing the problems. Since rework eliminates, the production stage takes less time and costs.
3. Relies on Data
Six Sigma in manufacturing completely relied on data associated with the manufacturing. The data involved are collected, analyzed, and used to improve the quality of the products. In addition, it improves the prediction rate with which future errors are foreseen. The data regarding the failures and wastes are kept for future reference in the production. Statistical data analysis improves the quality of output.
4. Increases Revenue
With Six Sigma implementation in manufacturing, the revenue to the business increases as part of the quality. Therefore, the implementation of Six Sigma increases the earnings of the company. The high standard products have a good market, improving the business’s revenue generation. In addition, since the waste is reduced to many numbers, they are converted into sales, increasing the business’s revenue.
5. Focus on Process Improvement
Since Six Sigma helps reduce the defects and flaws in the products, the focus on failure reduces. The focus is then moving to strategy and development of the business processes rather than fixing the current problems. Therefore, complete focus can be on improvement and innovative ideas for product development. Moreover, Six Sigma plays an important part in developing processes depending on customer requirements.
6. Improved Customer Satisfaction
The application of Six Sigma in manufacturing processes improves customer satisfaction. Customers are happier as quality improves and the number of defects decreases. It is a proactive approach rather than reacting after hearing back from the customers. When Six Sigma incorporates into production processes, product complaints will decrease.
We got some idea of the benefits of Six Sigma in manufacturing. Next, let us discuss some of the limitations in the manufacturing process due to Six Sigma.
Disadvantages – Six Sigma in Manufacturing
1. Focused Only on the Quality
Six Sigma implementation in the manufacturing industry will only focus on quality by reducing the number of defects identified. It may even lead to an increase in the production costs either directly or indirectly. In addition, there are chances of increasing the time consumed to manufacture a product. Thus, either one of the factors has to be traded with the six sigma implementation in the manufacturing processes.
2. Require More Resources
Since the Six Sigma implementation improves the mode of production with advanced technology products and testing methodologies, the resources required are higher. Apart from material resources, the need for highly skilled and experienced labor is also a drawback of the six sigma implementation. There will be a need for employees with Six Sigma belts called certifications to maintain the processes. Employees will also require training and guidance once Six Sigma introduce.
3. Addition of Production Costs
The production costs will increase with Six Sigma due to the additional technology products and experienced labor. An increase in production costs may be due to various reasons like an increase in labor costs, materials usage, and time taken for production. An increase in the production rate will increase the costs of the products. Therefore, there are chances that customers will look for low-priced products which are not suitable for Six Sigma and lean manufacturing.
4. Real-time Barriers
Apart from all these theoretical calculations, there are chances of other real-time issues. It is not secure that only 3.4 defects per million will encounter. There are chances of more barriers developing while in the production. These barriers are hard to predict as this will not be the same for every business. In addition, focusing on the development will have more such problems arising, and all of them require proper strategies to solve effectively.
We have discussed both the advantages and disadvantages. So, hope you got a clear understanding of the said points.
Conclusion
In conclusion, Six Sigma is a strategy for improving the quality of manufacturing processes by lowering the number of defects found. It is a proactive approach rather than reacting to the identified errors. Six Sigma helps to improve the quality and standards of production and products. It integrates with Lean manufacturing to create Lean Six Sigma, which reduces lean waste during the production process. It also provides opportunities for process improvement and working towards innovation in the products. Though there are several Six Sigma in Manufacturing | Advantages & Disadvantages. The drawbacks here are mainly based on increased costs due to increased quality. With the six sigma implementation, the manufacturing industry has foreseen several benefits rather than these drawbacks.
Invensis Learning is a great platform to upskill yourself with Six Sigma certifications. At Invensis Learning, we provide live sessions and plenty of resources to support. So, check out the courses on our Invensislearning.com website. In addition, we provide various certifications like
- Lean Six Sigma Yellow Belt Certification
- Lean Six Sigma Green Belt Certification
- Six Sigma Awareness Certification
- Six Sigma Black Belt etc.
With a 97% success rate at Invensis Learning, we assure you will get certified with essential skills in Lean Six Sigma.