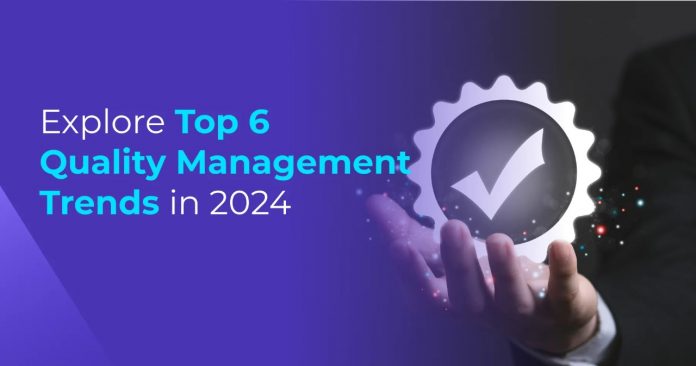
As we step into 2024, the world of quality management is undergoing transformative shifts that promise to redefine the way organizations operate, innovate, and excel. Are you curious to know which trends are shaping the future of quality management and how they could impact your industry or role?
Our latest blog on top quality management trends offers a unique blend of insights, predictions, and actionable strategies that are to be noticed. You will also explore the shift towards strategic quality planning and building a collaborative culture of excellence within your team
Learn how to integrate customer feedback for continuous improvement and leverage data analytics for proactive decision-making.
Stop struggling and start exceeding expectations!
Table of Contents
- Agile and Lean Quality Management
- Customer Centric Quality Management
- Strict Supplier Specific Quality Standards
- Tech-Driven Continuous Learning and Improvement
- Zero Waste Strategies
- Future Ready Quality Management
Top 6 Quality Management Trends to Know in 2024
Quality management is constantly evolving, driven by innovation and the ever-growing demands of customers. In 2024, several key emerging trends promise to revolutionize how businesses approach quality assurance.
These trends leverage cutting-edge technologies, prioritize customer experience, and emphasize proactive planning. By embracing these advancements, organizations can streamline processes, gain deeper quality insights, and ultimately deliver products and services that consistently exceed expectations.
Let’s explore the top 6 trends that will define quality management in 2024.
-
Agile and Lean Quality Management
The traditional approach to the quality management system is giving way to a more dynamic and collaborative method: Agile and Lean Quality Management. This powerful combination merges the iterative nature of Agile development with the waste-elimination principles of Lean thinking.
The integration of Agile and Lean methodologies is revolutionizing quality management. Agile quality management promotes flexibility and collaboration, enabling organizations to adapt quickly to customer feedback and deliver high-quality outcomes in shorter cycles. Meanwhile,
Lean quality management focuses on eliminating waste and optimizing processes to maximize customer value. These approaches foster agility, efficiency, and customer-centricity, making them essential trends that organizations should embrace to achieve competitive advantage in the ever-changing world of business.
By combining these approaches, teams can achieve several benefits:
- Faster Delivery: Agile practices enable quicker iterations and faster feedback loops, allowing products to reach the market shortly
- Reduce Costs: Eliminating waste in quality processes minimizes rework and resource expenditure
- Improve Customer Satisfaction: Continuous integration of customer feedback ensures products align with their needs and expectations
- Enhance Team Collaboration: Lean and Agile principles foster a more collaborative work environment where all stakeholders are actively involved in quality assurance
Enroll in our Quality Management certification courses and master the upcoming Quality Management trend!
-
Customer Centric Quality Management
Customer-centric quality management is a big trend that focuses on putting customers first when it comes to quality. Instead of just checking products or services for defects, this approach listens to what customers want and need.
By using customer feedback and data, companies can better understand these needs and make improvements before problems arise.
This customer-focused approach helps companies be more proactive. It means they can fix issues quickly and make products or services that customers love.
In a world where customers have many choices, being customer-centric in quality management can help companies stand out, build loyalty, and succeed in the long run.
The benefits of Customer-centric quality management are plentiful:
- Improve Customer Loyalty: By actively addressing customer concerns and exceeding expectations, brands can build stronger customer loyalty and foster long-term relationships
- Enhance Brand Reputation: Positive customer experiences create positive word-of-mouth marketing, boosting brand reputation and attracting new customers
- Data-Driven Decision Making: Customer feedback provides valuable data that can be used to make informed decisions about product development, marketing strategies, and overall quality improvement initiatives
- Increase Innovation: Understanding customer needs allows organizations to develop innovative solutions that address real-world customer challenges, leading to a competitive edge.
-
Strict Supplier Specific Quality Standards
Suppliers play a vital role in maintaining the overall quality of their products and services. This trend means that companies are setting clear and specific quality rules for each supplier they work with.
Instead of using general standards for everyone, companies are tailoring their requirements to fit each supplier’s unique strengths and capabilities.
By doing this, companies can ensure consistent quality from their suppliers. It also helps suppliers understand exactly what is expected of them, which can lead to better collaboration and fewer misunderstandings.
Overall, this approach helps companies maintain high-quality standards in their products or services and build stronger relationships with their suppliers.
This quality standard approach brings several key benefits:
- Enhance Overall Quality: By ensuring your suppliers consistently deliver high-quality products, you elevate the overall quality of your offerings
- Reduce Costs: Mitigating risks associated with poor-quality supplies minimizes rework, production delays, and potential product recalls
- Improve Supply Chain Efficiency: Clear communication and collaboration with suppliers streamline the entire supply chain process
-
Tech-Driven Continuous Learning and Improvement
The future of quality management is powered by intelligence. Tech-driven continuous learning and improvement leverages cutting-edge technologies to automate tasks, unlock hidden insights, and accelerate the process of continuous improvement.
This approach uses advanced technologies like AI, machine learning, and data analytics to learn and optimize quality processes continuously. Organizations can proactively identify and address quality issues by analyzing real-time data, making informed decisions, and driving ongoing improvement.
This tech-driven approach also promotes a culture of continuous learning within organizations by providing employees with personalized training and real-time feedback.
By integrating technology and continuous learning into quality management practices, organizations can enhance agility, responsiveness, and competitiveness, ultimately delivering greater value to customers and stakeholders.
This data-driven approach unlocks a wealth of benefits:
- Faster Problem Identification: ML algorithms can detect subtle quality issues that might escape human detection, allowing for quicker intervention
- Proactive Quality Assurance: By anticipating potential problems, organizations can prevent defects before they occur, saving time and resources
- Data-Driven Decisions: Insights gleaned from quality data empower teams to make informed decisions about improvement initiatives, resource allocation, and overall quality strategy
- Continuous Learning: Technology facilitates a culture of continuous learning by providing real-time feedback and insights that can be used to refine and improve quality processes constantly
-
Zero Waste Strategies
Striving for excellence in quality often means tackling the twin challenges of reducing waste and maintaining eco-friendly production practices. Zero waste strategies aim to optimize resource use, minimize waste generation, and maximize the yield of quality products.
By leveraging data analytics and real-time monitoring, organizations can pinpoint waste hotspots and implement corrective measures swiftly.
Zero waste quality technologies drive efficiency and champion sustainability by reducing energy use, conserving water, and lowering emissions. This shift towards more eco-conscious production processes resonates with the growing demand for environmentally responsible products.
Furthermore, these technologies empower businesses to monitor and trace raw materials, ensuring adherence to environmental and ethical benchmarks.
The benefits of Zero Waste Strategies are distinct:
- Reduce Costs: Eliminating rework and waste saves money on materials, labor, and production delays
- Enhance Environmental Sustainability: Minimizing waste reduces your environmental footprint
- Improve Customer Satisfaction: By focusing on first-time quality, organizations deliver products and services that consistently meet customer expectations
- Increase Efficiency: Streamlined processes and optimized resource utilization lead to a more efficient and productive operation
-
Future Ready Quality Management
Future-ready quality management is a key trend that focuses on being prepared for what’s ahead in the business world. This approach encourages companies to keep an eye on what customers want, changes in the market, and new technologies that could affect quality.
It’s all about planning by thinking about different scenarios, identifying potential risks, and having backup plans in place to handle any challenges that might come up.
Future-ready quality management encourages companies to be open to new ideas and ways of doing things. By using the latest technologies and working together with others, companies can improve their operations, develop new solutions, and stay ahead of the competition.
In short, being “Future Ready” means being proactive, flexible, and ready to adapt to whatever the future brings to maintain high-quality standards and achieve long-term success.
The benefits of this future-proof approach are significant:
- Sustainable Competitive Advantage: By continuously adapting and improving, organizations can maintain a leading edge in the marketplace
- Enhance Resilience: Flexible quality systems allow organizations to navigate unforeseen challenges and disruptions more effectively
- Long-Term Customer Loyalty: A commitment to continuous improvement ensures products and services remain relevant and valuable to customers in the ever-evolving marketplace
Conclusion
The landscape of quality management is dynamic and constantly evolving to meet the ever-changing needs of businesses and customers. As 2024 unfolds, several key emerging trends promise to revolutionize how organizations approach quality assurance.
These trends leverage cutting-edge technology, prioritize the customer experience, and emphasize proactive planning. By embracing these advancements, organizations can streamline processes, gain deeper quality insights, and ultimately deliver products and services that consistently exceed expectations.
By embracing these trends, organizations can transform their quality practices and achieve operational excellence.
Are you passionate about driving excellence, optimizing processes, and ensuring customer satisfaction? Invensis Learning’s Quality Management certification courses are the perfect choice. We offer a range of courses, from Lean Six Sigma to Customer-Centric Quality, all taught by industry experts. Future-proof your quality skills! Visit Invensis Learning today and unlock operational excellence in 2024.