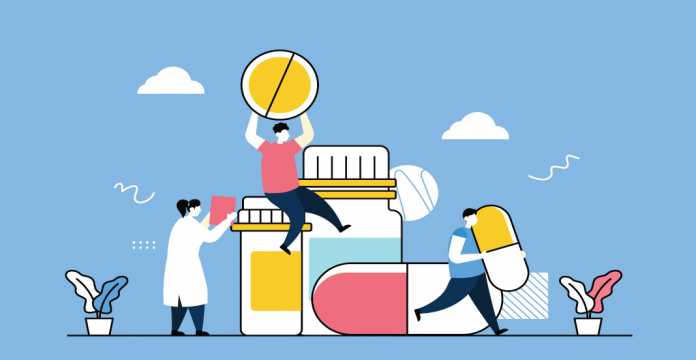
Pharmaceutical companies need to be extra careful and vigilant when it comes to quality control of their product. This is why they take the pharmaceutical Quality by Design (QbD) approach. The Quality by Design approach handles development based on sound science using quality risk management for their products. The pharma industry uses QbD for development by starting with a set of predefined objectives. Then it moves on to creating a strong emphasis on understanding the product and process control.
The Quality by Design approach is being put to use to make sure the products of pharmaceutical companies are safe and effective and that their supply is of high quality for the consumer’s use. QbD also ends up improving the performance and quality of manufacturing significantly.
The Development Process of the Quality by Design Approach
There are a few steps to development used by the Quality by Design approach. This development process includes the following:
Create a Target Product Profile
The first phase of the QbD process is to create a target product profile. This profile will include a thorough description of how the product will be put to use, the safety measures included, and the overall efficacy of the final product. This target product quality profile will be used as a guide for all aspects of clinical safety while the product is in development by process engineers as well as formulators.
Define the Target Product Profile
All information about the drug substance, process operations as well as potential excipients are collected in one space and a risk assessment is conducted to find any knowledge gaps that need to be investigated.
Design the Critical Attributes and Process Parameters
The next step in the development process is to design and formulate all the attributes that the final product needs to include by identifying the critical material involved. These attributes are listed to be controlled so that they can meet the target profile created.
All critical process parameters need to be identified as well so that a proper manufacturing process can be established. These parameters will include all the material attributes created and all other raw material attributes themselves. The risk assessment will be conducted so that all process parameters and raw material attributes can be prioritized and verified for experiments.
The combination of collected data and experiments will help create a design space to understand the overall process better.
Create a Control Strategy
After all the parameters have been set and experiments have been established, the next step in the QbD process is to create a control strategy that can be used for the entire process. This can include the following aspects:
- Listed input material controls
- All process controls and monitors
- Design spaces that are to be used for individual as well as multiple-unit operations
- Final product tests
This control strategy needs to include changes that may be required to make the production scalable as well. A risk assessment for the same will help guide the expected changes here.
Monitor and Update the Process on a Regular Basis
Regular assessments need to be in place to make sure all the products are of consistent quality. Some of the common assessments used in the QbD process to ensure quality are:
- Design of experiments (DOE)
- Risk assessment
- Process analytical technology (PAT)
FDA for Quality by Design in the Pharmaceutical Industry
QbD has become a big part of quality assurance processes in the pharmaceutical industry, so much so that even the United States FDA has taken an initiative and adopted QbD principles for their manufacturing of drugs as well as its discovery and development.
FDA has also released multiple guides to help the pharma industry to help them implement QbD in their processes. This helps create a standardized measure of quality for all drug companies across the country. It focuses on maintaining a certain level of quality and creating a better understanding of the product and the processes for its development as well as manufacturing. It also focuses on creating a better understanding of the risks involved while manufacturing and gives proper insight on how to approach and manage these risks.
Another benefit that pharma companies receive after the involvement of the FDA in the QbD approach is that it provides a design space for manufacturing. It will help in the scaling of commercial manufacturing of products by giving organizations accurate information about the processes and interactions involving the raw materials used in manufacturing. Companies will continue to benefit from this knowledge and improve regularly because they will be adapting to all manufacturing problems and addressing them periodically in a structured manner.
Elements of Quality by Design
There are many elements involved in the overall QbD process, which are:
- Quality Target Product Profile (QTPP): QTPP helps identify various CQAs of the product
- Product design: This creates understanding and the identification of CMAs
- Process design: This includes the understanding and identification of process parameters CPPs and different principles involving scaling, which link the CMAs and CPPs to CQAs
- Control strategy: this includes details of the following
– Drug substances
– Excipients
– Drug product
– Controls for all the steps involved in manufacturing - Process capability
- Continual improvement
Advantages of Using a QbD Approach
Continuous Improvement in Manufacturing and Quality
QbD can be a guaranteed way of making sure that the pharma drugs are safe and effective. The approach also helps with improving the quality of the overall manufacturing process. Pharma companies have to improve their strategies for development regularly and make changes whenever any issues need to be corrected. QbD can be used to guarantee the reliable performance of the product because it is backed up by statistical tools and optimal process conditions.
Support for Change
QbD is a scalable and highly adaptable approach because the parameters to ensure quality is created in the development phase of the product itself. All updates, variations, and changes that need to be made only require minor modifications. This means the QbD approach creates a space that supports any changes.
The design space created has a varied multi-dimensional approach to combining and interacting with input variables as well as process parameters. All changes that need to be made can be made in this created design space so that all quality requirements can be met easily.
This way necessary changes can be made in the process easily without impacting the characteristics of the final product.
Prevention of Failure
Since QbD gives pharma companies a total understanding of the parameters involved in the development, they can easily assess risks throughout the development cycle of the product and then mitigate or eliminate them accordingly. This reduces the chances of failure to an absolute bare minimum and companies can easily achieve accurate and consistent results to deliver their target value.
Consistency in the Product
Since QbD is a measure of quality, it can also be considered a measure for delivering with consistency. Constant vigilance when it comes to quality assurance results to achieve consistent results as a by-product. The process and product both get fortified over time and the overall complexity in the development and manufacturing process gets reduced greatly. This ensures consistency in medication delivered to consumers.
Final Thoughts
QbD is a forward-thinking approach to the manufacturing and development of drugs in the pharmaceutical industry. The faster this approach gets implemented globally, the more sound and responsive the consumers will be when it comes to developing trust in pharma companies worldwide. Training pharma employees in widely-recognized Quality Management Certification training programs will help them to adhere to the Quality by Design approach, and all processes involved in the development and manufacturing become a lot more simplified and standardized.
Some of the popular quality management courses through which the workforce can get trained to remove different types of waste in an organization are:
Quality by Design (QbD) Training
Lean Six Sigma Green Belt Certification
Six Sigma Black Belt Certification