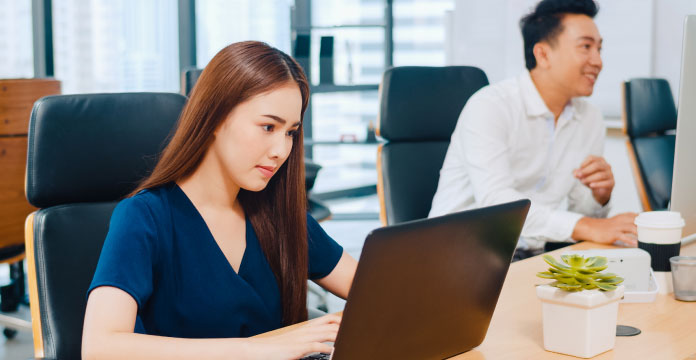
Lean Six Sigma is one of the leading process excellence programs in the world. A large number of professionals strive to achieve a competitive advantage by seeking qualifications in Lean Six Sigma Green Belt. This allows the professionals to be well-versed in state-of-the-art concepts, techniques, tools, and methods within Lean Six Sigma methodologies which help them in playing an important part in the contributions of commercial and industrial organizations worldwide.
Process excellence comes in the domain of Lean and Six Sigma and is all about process efficiency and effectiveness and involves designing and bringing about improvements in the processes in order to increase consistency in delivery with the least variation and minimum waste. An organization’s success or failure is largely determined by the effectiveness of the processes which form the foundational base of nearly all businesses. The key to maintaining profitable relationships is the ability of organizations to seamlessly guide internal resources and customers through sales, billing, onboarding, support, and various other critical business processes.
For a business enterprise to truly achieve process excellence, it has to have a clear understanding of the type of improvement program to pursue, clearly define the program goals and find the most effective way to integrate myriad technology into these efforts.
Using Lean Six Sigma for Process Excellence
For business enterprises to derive value from improvement initiatives, they have to shift their primary focus from basic methods and tools. Lean plays an important role in providing powerful tools that identify and eliminate waste from processes thereby reducing cycle times. Six Sigma, on the other hand, is a set of strategies and tools that help in limiting defects and inconsistencies in business processes with the ultimate goal of process improvement. Various organizations have adopted Lean and Six Sigma techniques but only a small percentage of the initiatives are reaching their full potential. There are three core doctrines for bringing about business transformation:
- Lean Leaders as role models to truly empower the workforce
- Aligning initiatives to principal business strategy to ensure improvements
- To create targets that are aimed toward service level competitiveness and not just cost reduction
Leaders Must Bring About Change-Lean Leadership Maturity Model:
The lean Leadership model mainly expresses how Lean deployment evolved in most organizations. The quintessential Lean Leader is the one who creates a learning culture entirely based on the creation of customer value at the least possible cost. The leader can work cross-functionally and collaboratively in the complete value stream of the organization and has recognized that it is the right time to devise a system that will effectively leverage people, maximize customer value and eliminate waste.
Leaders must be always open to change and learning and influence those around them by creating a learning environment. This is the main reason why using Lean and Six Sigma tools in isolation does not deliver long-term operational transformation. These tools must be instead used as a part of a wider methodology to drive continuous improvement.
Strong results can be achieved by deploying rigorous tools, standards, and audits but in the longer run, improvements and results only slow down. Therefore, a different approach must be taken up by the leadership and the main focus should be on strengthening Lean behaviors through on-the-job training. The top priority must be supporting continuous improvement and training teams, which if done effectively can be truly transformational.
Breaking Down Organizational Silos:
Working in outdated, functional specialist silos is one of the biggest obstacles to achieving process excellence. Software companies witness an excess of functional silos. These include programming language expertise, development work, and various other silos that promote expertise in their own niche. In spite of all this expert domain knowledge, the resulting software rarely solves the problems of business users. According to research, close to 68% of software projects do not deliver anticipated business benefits and the main reason behind this is organizational silos.
Senior leaders in a team are frequently considered a unique group of high-performing individuals and their main area of interest is financial performance which in reality is immaterial when it comes to day-to-day operations. The main aim should be business transformation. The goal must be to bring about performance improvements in the value stream and set up a rewarding workplace for the employees. The result will be that the organization’s performance will improve thereby creating a platform for continuous improvement. Improvement activities can be directly related to business results by directly integrating business transformation governance with a business performance management system. Business targets can be successfully met if teams work in tandem to reduce risks and successfully implement improvement initiatives.
For the above-mentioned steps to work effectively, leaders must be open to change and learning and create a learning environment for all the other employees around them. If various levels of the organization are not equally involved business transformation cannot be successful.
Which Organizations can Deliver Change Best?
Organizations that are successful in delivering change are usually the ones that practice consistency in their approach and have strong values when it comes to implementing change, mainly focusing on long-term impacts. Leadership behaviors should be consistent right from executives to managers to team leaders and the behaviors must be supportive of the organization’s values and be specific to the organization’s workings. If an organization hopes to create a consistent and high-performing working culture to deliver breakthrough performance, it must not have several standards of leadership behavior.