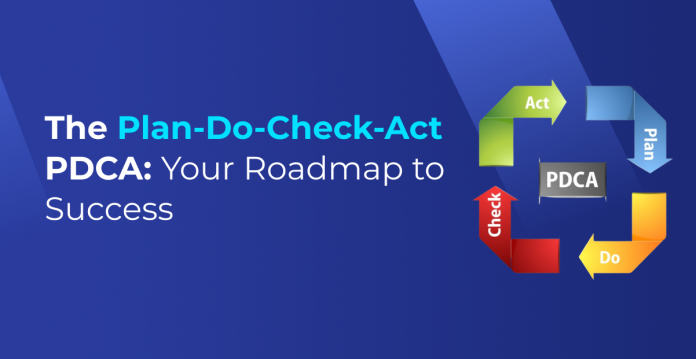
Most businesses want to get better, but turning that desire into actual improvements can be hard. Things like too many rules, separate working groups, and a fixed way of doing things can get in the way and stop new ideas. That’s where the Plan-Do-Check-Act (PDCA) model comes in. It’s like a special plan that helps businesses not get stuck.
PDCA is a step-by-step way to keep getting better all the time.
It’s a great tool to break through challenges and ensure your business is always moving forward.
Learn more about how PDCA works and all the good things it can bring to your company’s growth.
Table of Contents
- What is Plan Do Check Act (PDCA) Cycle?
- When to Use PDCA Cycle?
- Plan Do Check Act Example
- Pros and Cons of PDCA
- The PDCA Model-Explained
- Conclusion
What is Plan Do Check Act (PDCA) Cycle?
Plan-Do-Check-Act (PDCA) is a four-step management method used for continuous improvement in processes, products, or services. Also known as the Deming Cycle or Shewhart Cycle, PDCA is a systematic and iterative approach to problem-solving and quality improvement. The four steps in the PDCA cycle are:
- Plan: Identify the problem or opportunity and plan for improvement. Set objectives, define processes, and establish metrics for success.
- Do: Implement the plan on a small scale. Execute the planned changes and collect data for analysis. This phase involves carrying out the proposed changes or solutions.
- Check: Evaluate the results by comparing data collected during the “Do” phase with the objectives set in the “Plan” phase. Assess whether the changes have led to improvement or if adjustments are needed.
- Act: If the results are satisfactory, standardize the changes and integrate them into the regular processes. If improvements are still needed, return to the planning phase, adjust the plan based on the lessons learned, and repeat the cycle.
When to use the PDCA cycle?
The PDCA cycle is valuable for addressing project management and process improvement challenges. Its versatility allows for widespread application across diverse projects.
Teams that effectively incorporate the PDCA cycle foster a culture of continuous improvement. Instead of viewing the cycle as a linear process, it becomes a means to ensure ongoing refinement through an iterative approach.
The PDCA cycle finds application in various aspects of business to bolster efficiency and deliver improved outcomes. It is particularly useful for:
- Project Management: Employing PDCA ensures systematic problem-solving and continuous improvement throughout project lifecycles.
- Customer Service Enhancement: Enhancing the quality of customer service is pivotal for organizational success. PDCA provides a structured method to identify, analyze, and improve customer service processes.
- Risk Management: PDCA is instrumental in identifying and mitigating risks within various business processes, ensuring proactive risk management.
- Employee Training and Development: Utilizing the PDCA cycle for managing employee training and development programs ensures continuous improvement in skill-building initiatives.
- Marketing Campaign Optimization: PDCA can be applied to analyze and refine marketing strategies, optimizing campaigns for better reach and effectiveness.
- Financial Planning and Budgeting: The PDCA model effectively manages financial processes, allowing organizations to adapt and optimize budgetary allocations for improved financial performance.
Master PDCA cycle by enrolling in Invensis Learning’s Quality Management courses Now!
Plan Do Check ‘Act Example
Embark on a journey of operational excellence as we delve into a real-world example illustrating the Plan-Do-Check-Act (PDCA) cycle. Explore the stages of planning, execution, evaluation, and refinement through a compelling case study, showcasing how organizations leverage PDCA for continuous improvement and strategic optimization.
Plan
A manufacturing company aiming to enhance product quality initiates the PDCA cycle for its assembly line processes. The plan involves:
- Identifying quality issues through customer feedback and internal analysis.
- Setting a target to reduce product defects by 15% within the next production cycle.
- Planning-specific measures include enhanced quality control checks, employee training on quality standards, and improving manufacturing equipment maintenance.
Do
The manufacturing team implements the planned changes, including:
- Introducing additional quality checkpoints in the assembly line.
- Conducting training sessions for assembly line workers on identifying and addressing potential defects.
- Implementing a preventive maintenance schedule for machinery to ensure consistent performance.
Check
Continuous monitoring and assessment of the outcomes occur:
- Regular inspections during the manufacturing process to identify and rectify potential defects.
- Analysis of defect rates through daily reports and quality control data.
- Gathering feedback from employees on the effectiveness of the new training initiatives.
Act
Based on the findings during the “Check” phase, the manufacturing team takes corrective actions:
- If the defect rate decreases as targeted, the changes are standardized, and the improved processes are integrated into regular operations.
- If certain measures prove less effective, adjustments are made. For instance, the team might refine the training program or modify the preventive maintenance schedule.
Pros and Cons of Plan Do Check Act
Pros
- Versatile Application: The PDCA cycle is adaptable to various business environments and can be applied to different projects, making it versatile for use in project management, change management, product development, and resource management.
- Simplicity and Power: The PDCA model is simple and easy to understand. Despite its simplicity, it remains a powerful tool for driving meaningful change and improvement, contributing to efficiency enhancement and waste reduction.
- Data-Driven Decision Making: PDCA emphasizes the importance of data collection and analysis at each stage. This promotes a culture of data-driven decision-making, allowing teams to base their actions on concrete evidence and measurable outcomes.
- Continuous Improvement Culture: PDCA fosters a culture of continuous improvement within an organization. By regularly revisiting and refining processes, teams become more adaptable, innovative, and better equipped to address evolving challenges.
Cons
- Challenging Implementation: While the model is straightforward, implementing PDCA can be challenging. Breaking down process improvements into smaller steps may result in slow progress, making it less suitable for urgent projects.
- Continuous Commitment Required: PDCA is not a one-time solution but an ongoing and continuous process. Sustaining its effectiveness requires a long-term commitment and buy-in from leadership at all levels. Without dedicated leadership, the PDCA cycle may struggle to function optimally.
- Resource Intensive: Implementing PDCA effectively may require significant time, effort, and resources. The cycle’s meticulous analysis and iterative nature demand a commitment of resources that might be challenging for organizations with limited capacity.
- Resistance to Change: PDCA involves making adjustments based on feedback and analysis, which can encounter resistance from individuals accustomed to existing processes. Overcoming this resistance and ensuring active participation is crucial for the success of the PDCA cycle.
The PDCA Model – Explained
Organizations can methodically address challenges and enhance processes by following the four-stage PDCA model. Let’s delve into each stage to understand how to implement the PDCA model effectively.
Plan
The planning stage focuses on meticulously mapping out strategies to address a problem or optimize a process. Start by identifying and analyzing the issue, formulating hypotheses for potential causes, and selecting one hypothesis for initial testing. Key questions to consider include:
- What is the core problem we need to solve?
- Is this the right problem to work on?
- What information do we need to understand the problem and its root cause fully?
- Is it possible to solve the problem?
- What resources do we need?
- What resources do we have?
- What are some viable solutions?
- What are the measures of success?
- How will the results from a small trial translate to a full-scale implementation?
Do
Moving on to the “Do” stage, it’s time to implement your planned solution. Focus on testing your hypothesis through a small-scale project in a controlled environment to minimize disruptions. The PDCA cycle emphasizes incremental changes, allowing for gradual process improvement.
Check
After completing the trial:
- Shift to the “Check” stage for a comprehensive review of the results.
- Evaluate the effectiveness of your solution and identify any unexpected challenges or improvements.
- Consider whether the plan worked as anticipated and analyze steps that could be enhanced or eliminated in future iterations.
This evaluation guides decision-making for the next steps in the PDCA cycle.
Act
The final stage is the “Act.” If the trial proves successful, you can implement the refined plan on a larger scale. Consider the resources needed for full-scale implementation, training for successful adoption, and metrics to measure and track performance. Reflect on opportunities for further improvement and extract lessons learned for application in future projects.
Conclusion
The Plan-Do-Check-Act (PDCA) framework is a powerful roadmap for success in various endeavors. Its versatility and simplicity empower individuals and organizations to systematically tackle challenges, foster continuous improvement, and optimize processes. By embracing the PDCA cycle, one navigates the path to success and cultivates a dynamic mindset that thrives on adaptability and innovation. As we reflect on the journey outlined by PDCA, its iterative nature becomes a beacon for sustained excellence, guiding us toward realizing goals and attaining success.
Elevate your expertise in Quality Management with Invensis Learning’s Certification courses. Take the next step towards mastering industry best practices and ensuring excellence in your professional journey. Enroll now to unlock a world of opportunities and advance your career in quality management!