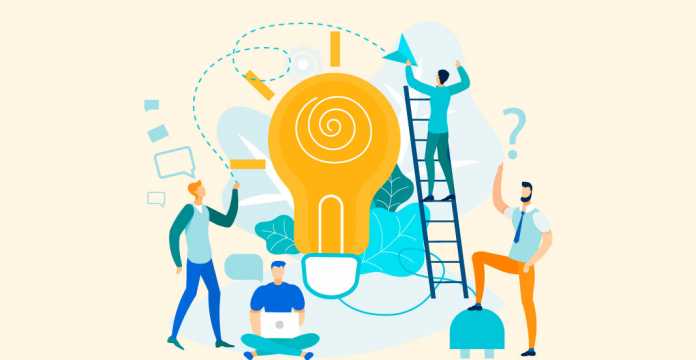
Six Sigma is a concept you’ve undoubtedly learned of regarding highly organized and profitable firms, but it might not be something you can readily identify. Six Sigma is certainly something you can hear about if you’re looking for a position in management. So, what are the primary goals of Six Sigma Implementation in an organization?

By integrating this philosophy into your company, your achievements can be radically transformed, and your customer loyalty improved.
What is Six Sigma?
Six Sigma was first used by Motorola in 1979 and is a way to improve quality by reducing errors and variation. It also aims at building a culture that is always striving to improve. This management concept is often coupled with Lean, another method of enhancing quality that aims to reduce organizational waste and inefficiencies to cut costs and boost productivity.
A Sigma value, or Sigma level, proves how often mistakes in a process are likely to occur. More specifically, it represents the number of errors per million possibilities — the higher the Sigma, the lesser errors. Six Sigma is the highest level on the Sigma scale, going to represent only 3.4 defects or errors for every one million opportunities, whereas one Sigma is the lowest;
Primary Goals of Six Sigma
Any organization that seeks to implement Six Sigma or any enhancement program should have a clear understanding of what it expects the action plan to achieve. Instead of abstract thinking, such as ‘we want to get better,’ project leadership needs to set clear and achievable targets that can be expected from the execution of any development strategy, even Six Sigma.
Six Sigma’s key objectives would include these particular results anticipated for the program:
Reduce Defects
Six Sigma’s target is to achieve a defect rate of six standard deviations from the norm or 3.4 defects per million goods, and it will educate six Sigma practitioners (green belts, black belts) to aim toward this degree.
This will not, however, be possible for all organizations and goods. Motorola invented Six Sigma, and General Electric popularised it, which produces several different interests. Consequently, it has been adopted as a basis for multiple development methods. Yet Six Sigma was questioned in that the six standard deviation law (six sigmas) is not uniformly valid to all sectors and goods. Many companies will refuse to reduce the defect rate to that level, since dealing with more defects is easier. A higher defect rate could attract customers too.
Quality
Quality management is one of the important primary goals of Six Sigma implementation. For practically every Six Sigma program, consistency is a natural, primary target. Without resolving quality problems in any phase, any more enhancement attempts will inevitably fall short. The major quality-related focus areas for standard Six Sigma initiatives include the elimination of errors/defects (or the proofing of errors) and the reduction of waste involved in manufacturing a good or service.
The project team will use a specified methodology and statistical methods to attempt to recognize and remove the causes of the defects in a given procedure. In doing so, the goal is to optimize the process’s final result with as few mistakes as possible. Secondary purposes related to consistency targets include improved consumer loyalty and enhanced profitability.
Know the Stats
Do you understand how many of your items are wrong or are your services short? If you know the consistency level as opposed to your competitors? If you know how to boost the efficiency of your service? Want to be higher than the average?
Implementation of Six Sigma would improve your numbers:
- Where the consistency of the product/service now is.
- Wherever you want to go
- How to get inside
- How to keep at it
- If nothing else, only the numbers you’ll know.
Variability
In this case, variability refers to the difference between the planned quality and the real performance of a product or service. Variance is sometimes, products or services that are not satisfactory to the end-user / client, and are refused resulting in excessive duplication, lower profits, and increased costs.
Variability may be caused by common causes (steady, random fluctuation) or by special causes (once, non-random fluctuation). Six Sigma aims to reduce uncertainty, resulting in stable processes generating consistent output.
Provide Career Advancement
Are you trying to keep people focused and deliver career growth targets that make them happy? Giving somebody a Six Sigma green belt or black belt certification training is a perfect way to keep them interested, practicing, and pushing their career forward. With the Six Sigma hierarchy structure in different colored belts representing enterprise structure, professionals can take up popular Six Sigma and Quality Management Courses to get ahead in their careers.
Improved Productivity
Rising efficiency is an overall goal for several implementations of Six Sigma. Also, small increases in a process’s productivity will bring significant advantages to the organization. Six Sigma ventures usually focus on reducing cycle time (the amount of time it takes to complete one processing process), such as a bank teller that serves a single customer. The longer the cycle time, the more cycles (clients) within a single shift can be handled.
Other areas of change include eliminating measures that are duplicative or don’t add value to a process. The streamlining of the processes tends to maximize processing time and minimize idle time, thereby enhancing the total process efficiency.
Improve Corporate Culture
Perhaps a few individuals will become Six Sigma Yellow, Green, or Black Belts but this acts as a precedence for the entire organization which will see the quality emphasized throughout the organization. Implementing Six Sigma is an obvious way to say that “safety matters” to everyone. That’s a value you can’t quickly put a price on.
So these are the primary goals of Six Sigma Implementation in any organization.
How to Implement Six Sigma?
The first phase in every Six Sigma project is obtaining buy-in from those concerned. “It is crucial to engage all staff levels in the method to make better results. Lean six sigma methods in the manufacturing sector will enhance production rates and reduce delivery times.”
One of the key aspects while implementing Six Sigma in an organization is to identify a leader who has Six Sigma experience. The best way to start is to go small, by identifying a project where Six Sigma best practices can be introduced. Later, with lessons learned the same can be applied to a business-critical project to obtain better value for the organization.
Keys to Six Sigma Success in the Real-world Scenario Include:
- Identifying a specialist in Six Sigma principles
- Proper communication with the team during the whole process
- Adequate preparation for the experimental employees
- Modify strategic techniques
- Workplace cultural change
To get a better understanding of Six Sigma and its benefits, it’s recommended to pursue popular Lean Six Sigma Certification courses from an IASSC-accredited training provider.