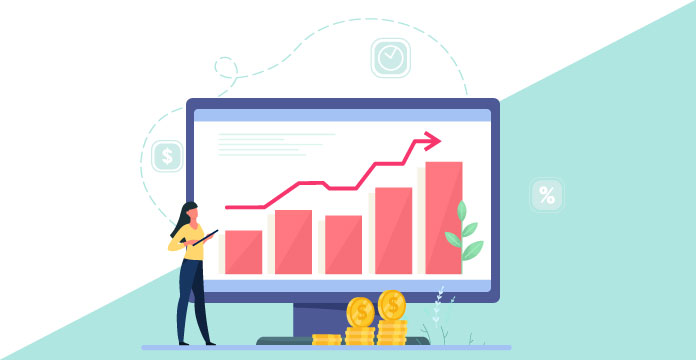
Since the end of the Second World War, Kaizen has been adopted by both massive multinational and small firms in Japan. Productive work and efficiency require a clean atmosphere, protection, and discipline. So, Kaizen’s Japanese philosophy is simple and successful for tidiness. Many organizations have adopted the Lean methodology, and Kaizen is one of the essential pillars of this methodology.
What is Kaizen Methodology?
Kaizen is a term used in Japanese, which means “Continuous Improvement” – making changes for the better. But the better way to understand Kaizen is not just any kind of improvement. But small improvements for the better. Kaizen is incremental. i.e., Small progress that over time amounts to extraordinary results. Kaizen Methodology is an approach that promotes continuous improvement in the enterprise, focused on continual small positive improvements that can lead to utmost and more substantial growth.
Kaizen refers to practices in a company that constantly enhance all functions and include all staff from the CEO to the assembly line workers. As part of the lean process enhancements, Kaizen considers a culture rather than a methodology, focused on collaboration and cooperation between the company’s members.
Benefits of Kaizen
- Continuous minor changes add up to significant advantages. They lead to increased efficiency, improved quality, improved safety, quicker delivery, lower costs, and greater customer satisfaction
- In addition to these benefits for the business, workers employed in Kaizen-based companies typically find work more straightforward and more pleasant, resulting in more excellent employees morale and job satisfaction and lower turnover
- In areas such as waiting times, employee skills, transport, worker mobility, overproduction, excess inventory, quality, and procedures, Kaizen eliminates waste
- Kaizen enhances product quality, resource usage, manufacturing capability, communications, space use, and employee retention
- Kaizen gives immediate results. Instead of concentrating on capital-intensive, large-scale upgrades, it focuses on innovative investments that continuously solve large numbers of small problems
- In the process of transition, Kaizen includes every employee – often in minor, incremental changes. It focuses on finding issues at its own source, fixing them there, and changing standards to ensure that the problem is forever solved
Are Kaizen and Lean The Same?
Kaizen and Lean are words that are frequently interchangeably used but are two distinct entities. Lean focuses on waste prevention and increasing consumer productivity and value, while Kaizen emphasizes continuous improvement. As a Lean business tool, Kaizen emphasizes performance only when all workers search for ways to develop and offer feedback based on their insights and experience.
Fundamental Principles of Kaizen
Kaizen is focused on the concepts as follows:
- Team Effort: The most substantial assets are people. Teamwork results in higher results and helps everyone feel happy
- Good Processes: Kaizen believes that good procedures offer good outcomes. If any department performs badly, it’s not the employees who are at fault in the process
- Focus on Small, Continuous Changes: People need to be open to enhancements and improvement. Management ideas, staff, clients, and suppliers will contribute to simpler, fresh, and improved ways of doing things
- See it to believe it: Kaizen practice advises you to visit the place of service to see the issues faced, and procedures followed firsthand
- Elimination of Waste: The fundamental goal of Kaizen is to remove waste called “Muda.” This guides a company to define these three MUs: Muda, Mura, and Muri
- Muda implies wastefulness, uselessness, and futility, which contradicts the addition of value
- Mura means unevenness, irregularity, and non-uniformity
- Beyond one’s power, excessiveness, impossible or unreasonable, Muri means overburden
Here’s a picture showing the distinction between the three:
How is Kaizen Methodology Implemented?
Step 1: Involve Your Employees
You need to include your employers first, which will allow you to empower your employees. You need your workers inspired and involved to implement Kaizen. You want to build a workplace that does not oppose change and is genuinely responsible for the change. To do this, you need your staff’s full cooperation, and contact between management and employees is essential.
Kaizen has the idea of Quality Circles, in which there are specific circles of employees from different departments responsible for the overall development of the business, slowly but steadily.
Step 2: Analyze the Process
The second step to Kaizen is to accept and identify issues in your organization. To do this, you need to take 360-degree feedback and include your staff. It would help if you listed all processes within the company that need improvement.
Step 3: Think & Find Solutions
Managers should make teams of accomplished, innovative workers who can concentrate on problem-solving. They will have to devote extra time to seeking solutions to the issues that the company is facing.
The time frame is very important. We want solutions to come forward comfortably and innovatively and not to throw down any proposals because they can come later, even if they are not fully utilized and implemented. Write down the solutions, and use your expertise and a team experience to make the most sense of the suggestions. You should then make these recommendations for implementation.
Step 4: Implement the Solution
Small-scale implementation is the best way, especially in larger organizations, to test new theories. Many people are delaying this stage because of overthinking, complacency, or simple ignorance. They are thinking about making organizational improvements instead of taking small steps at a time and running new ideas in a pilot environment.
If the ideas need to evolve a little further, keep the enthusiasm, and improve the table’s concept before implementing it in the company. However, a concept must have a planned and monitored implementation so that the effects can be tracked.
Step 5: Study the Results
There is an open discussion of ideas among juniors several times during implementation, whereby the buck is transferred to someone else. This is what makes it challenging to enforce Kaizen and where it comes into play with testing and auditing. For the outcomes to be right, you need to ensure that implementation is achieved at the ground level.
Step 6: Standardize the Solution
You need to go back to the 3rd stage if the results are not positive, in which you introduce some other ideas that were on the table. Do not get upset and annoyed because Kaizen has many advantages, and you will find the advantages slowly but steadily.
However, if the outcomes are good and you see the process improving, then standardize the process in all divisions and all locations by all means so that the company operates more smoothly and efficiently. The best advantage of introducing Kaizen is standardization.
Step 7: Repeat
Repeat the entire process so that it is possible to optimize further practices. “Continuous improvement” and “slow and gradual change” is the true essence of Kaizen. Kaizen simply means “Change is a good thing.”
So, now you guys know about Kaizen methodology.
Final Thoughts
There are several benefits to the adoption of kaizen principles. Solutions emphasize common sense, low-cost methods, constant adjustment, and development is possible and desirable. To make adjustments, it is not necessarily appropriate to seek upper management approval. Kaizen includes everybody in the effort to change things. It does not rely on massive capital expenditures, nor does it seek to make tremendous strides at one time. Toyota is perhaps the most popular company to use Kaizen.
Putting together a strong team of well-trained individuals in some of the popular Quality Management Certification Training programs to incorporate new and innovative practices is really important. Incorporating the Lean Six Sigma methods could only lead to long-term success.
Some of the popular Quality Management Certification courses that individuals and enterprise team members can take up are: