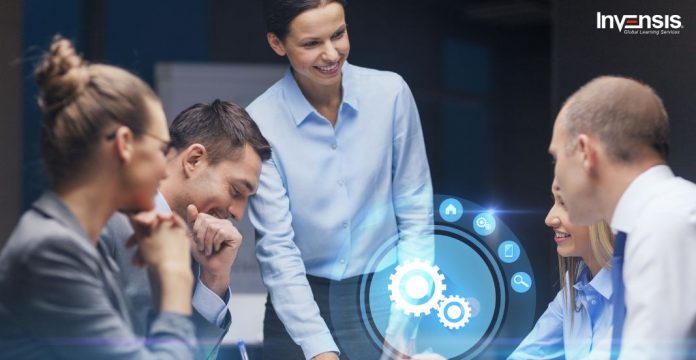
Employee engagement is a critical factor in the success of any organization. Engaged employees are more productive, innovative, and motivated, which leads to better business results. However, many organizations need help to maintain high levels of engagement among their workforce. This is where Six Sigma, a data-driven quality improvement methodology, can help. Organizations can use the Six Sigma methodology to identify and eliminate the root causes of low employee engagement, resulting in increased job satisfaction and a more motivated workforce. In this blog, we will explore how Six Sigma can improve employee engagement and provide a step-by-step guide for implementation.
Understanding Employee Engagement
Employee engagement refers to employees’ commitment, motivation, and involvement in their work. It measures employees’ investment in their jobs, the organization, and goals. Engaged employees are characterized by high energy, enthusiasm, and dedication and tend to be more productive, innovative, and motivated.
An engaged workforce is a key driver of organizational success, as it can lead to increased productivity, better customer satisfaction, and improved financial performance. Conversely, low employee engagement can result in decreased productivity, increased absenteeism, and higher turnover rates, which can significantly impact the bottom line.
Various factors can influence employee engagement, including job satisfaction, work-life balance, job security, and recognition and rewards. Effective engagement strategies focus on creating a positive work environment, providing opportunities for professional growth, and fostering a culture of open communication and collaboration.
The Relationship Between Six Sigma and Employee Engagement
Six Sigma and employee engagement are closely related concepts that can significantly impact organizational success. Six Sigma is a data-driven quality improvement methodology that eliminates defects and improves processes. It focuses on continuous improvement, data analysis, and customer satisfaction and is widely used in the manufacturing, service, and healthcare industries.
On the other hand, employee engagement refers to employees’ commitment, motivation, and involvement in their work. Engaged employees are more productive, innovative, and motivated, which leads to better business results. On the other hand, a disengaged workforce can lead to decreased productivity, increased absenteeism, and higher turnover rates.
The relationship between Six Sigma and employee engagement can be understood through the Six Sigma DMAIC (Define, Measure, Analyze, Improve, Control) process. The DMAIC process provides a structured approach for identifying and eliminating the root causes of low employee engagement. Organizations can use data and statistical analysis to determine the factors affecting employee engagement and implement improvements to increase engagement levels.
For example, Six Sigma can be used to analyze the root causes of high turnover rates, a common indicator of low employee engagement. By collecting data on factors such as job satisfaction, work-life balance, and stress, organizations can identify the root causes of turnover and implement improvements to reduce turnover and increase engagement.
The relationship between Six Sigma and employee engagement is crucial for organizational success. Organizations can use Six Sigma to improve employee engagement by identifying and eliminating the root causes of low engagement and creating a more motivated and productive workforce.
How can the DMAIC Process be Applied to Improve Employee Engagement?
The DMAIC (Define, Measure, Analyze, Improve, Control) process is a key component of the Six Sigma methodology and can improve employee engagement. Here’s how the DMAIC process can be applied to this goal:
Here’s a table that outlines the DMAIC process as applied to improving employee engagement:
DMAIC Step | Description |
Define | The problem or opportunity related to employee engagement you want to improve. For example, you can improve job satisfaction or reduce turnover rates. |
Measure | Collect data on employee engagement using surveys, interviews, or other metrics. This data will be used to determine the current engagement level and track progress over time. |
Analyze | Use statistical tools to analyze the data collected in the measure phase. Identify trends, correlations, and root causes of low engagement levels. |
Improve | Develop, and implement solutions to address the root causes of low engagement. This could include changes to work processes, improvements to the work environment, or new employee engagement programs. |
Control | Monitor and evaluate the results of the improvement efforts and make ongoing improvements as needed. This will ensure that employee engagement remains high over time. |
And here’s a sample table that summarizes the data collected and analyzed in the Measure and Analyze steps of the DMAIC process:
Data Category | Data Point | Data Collection Method |
Job Satisfaction | Percentage of employees who rate their job as satisfying | Employee Survey |
Work-Life Balance | Percentage of employees who feel that their work and personal life are balanced | Employee Survey |
Job Stress | Percentage of employees who feel that their job is stressful | Employee Survey |
Turnover Rates | Percentage of employees who have left the company in the past year | Human Resources Data |
By using tables like these, organizations can clearly outline the data they have collected and analyzed, making it easier to understand the root causes of low engagement and implement improvements to increase engagement levels.
Examples of Organizations Successfully Using Six Sigma to Improve Employee Engagement
Toyota
Toyota used Six Sigma as a problem-solving methodology to improve its operations, including employee engagement. The company applied the DMAIC (Define, Measure, Analyze, Improve, Control) process to understand and address the root causes of low employee engagement levels. The Six Sigma approach helped Toyota collect and analyze employee satisfaction data, identify improvement areas, implement changes, and measure their impact. Through this process, Toyota created a more positive work environment, increased employee satisfaction and motivation, and ultimately enhanced employee engagement.
Outcomes and Benefits
Implementing Six Sigma at Toyota led to several outcomes and benefits in improving employee engagement. Some of the most notable ones are
- Increased employee involvement: By involving employees in the problem-solving and improvement process, Toyota could tap into their collective expertise and experience, which led to more innovative and effective solutions.
- Improved communication and collaboration: Six Sigma fosters a team-based approach emphasizing clear communication, collaboration, and teamwork. This helped to break down silos and build stronger relationships between different departments and functions within the company.
- Increased job satisfaction: By giving employees a sense of purpose, ownership, and meaning in their work, Toyota was able to improve employee satisfaction, which led to higher levels of engagement, motivation, and commitment.
- Improved process efficiency: Six Sigma helped Toyota streamline processes, reduce waste and improve quality, freeing up time and resources that employees could use to focus on more strategic and value-adding activities.
- Improved financial performance: By improving the efficiency, quality, and reliability of its processes, Toyota was able to reduce costs, improve productivity, and increase profitability. These financial benefits are fed into the company, boosting employee morale and motivation.
Implementing Six Sigma at Toyota contributed to a more engaged, motivated, and productive workforce, supporting the company’s continued success and growth.
General Electric (GE)
General Electric (GE) implemented Six Sigma, a data-driven method for reducing defects and improving process efficiency, as part of a broader effort to improve employee engagement. Using Six Sigma to streamline processes and eliminate waste, GE aimed to create a more positive and productive work environment for its employees. Additionally, GE empowered employees to drive process improvement initiatives through the Six Sigma methodology, providing opportunities for skill development and career growth. As a result of these efforts, GE saw increased employee satisfaction and engagement and improved overall business performance.
Outcomes and Benefits
General Electric (GE) achieved several outcomes and benefits by implementing Six Sigma to improve employee engagement, including
- Increased efficiency: Six Sigma helps organizations streamline processes, reduce waste and minimize errors, leading to improved efficiency and productivity.
- Improved quality: Six Sigma focuses on data-driven problem solving, which can help identify and eliminate root causes of quality issues, improving overall quality.
- Increased employee satisfaction: By involving employees in the Six Sigma process and giving them a voice in identifying and solving problems, GE likely saw an increase in employee satisfaction and engagement.
- Cost savings: Six Sigma helps organizations identify and eliminate waste, leading to cost savings, which can be reinvested in other areas of the business.
- Improved customer satisfaction: By improving efficiency and quality, GE likely saw an increase in customer satisfaction, which can help improve the company’s overall reputation.
By implementing Six Sigma, GE likely saw improved business performance and increased employee engagement, which can help drive long-term success for the company.
Conclusion
Six Sigma can be a valuable tool for improving employee engagement. Organizations can foster a culture of engagement and empowerment by involving employees in problem-solving and giving them a voice. Six Sigma’s focus on data-driven problem-solving and continuous improvement can increase efficiency, quality, cost savings, and customer satisfaction. These outcomes can contribute to a positive work environment and ultimately drive long-term sauccess for the organization. By implementing Six Sigma, organizations can create a culture of engagement, improvement, and success, positively impacting employees and the organization.
Glossary
- Six Sigma: A data-driven, continuous improvement methodology that aims to reduce waste, minimize errors, and improve quality.
- Employee Engagement: It measures employees’ emotional and intellectual connection to work and organization.
- Efficiency: The ability to produce a desired outcome with the least waste of resources.
- Quality: The degree to which a product or service meets the customer’s expectations.
- Continuous Improvement: Continuously identifying and making changes to improve processes and outcomes.
- Root Cause Analysis: A problem-solving approach used to identify the underlying cause of a problem rather than just addressing its symptoms.
- Data-Driven: Reliant on or supported by data or evidence rather than assumptions or intuition.
- Cost Savings: The reduction in expenses incurred by a business, leading to increased profitability.
- Customer Satisfaction: The degree to which a customer is satisfied with a product or service.
————————————————————————————————————————————-Organize Corporate Group Six Sigma Certification training for your teams around the world
Invensis learning provides In-person and live virtual instructor-led corporate training program customized for enterprise teams who wish to train their employees on specific aspects of their job processes or responsibilities. The corporate training by our expert certified trainers will enhance your learning curve and enable your teams to utilize their skills to meet industry standards.
- Experienced & Industry Specific Trainers
- Lifetime LMS access
- Deliver sessions across continents via In-Person/ Virtual Instructor-Led Training
- Customized Training————————————————————————————————————————————-