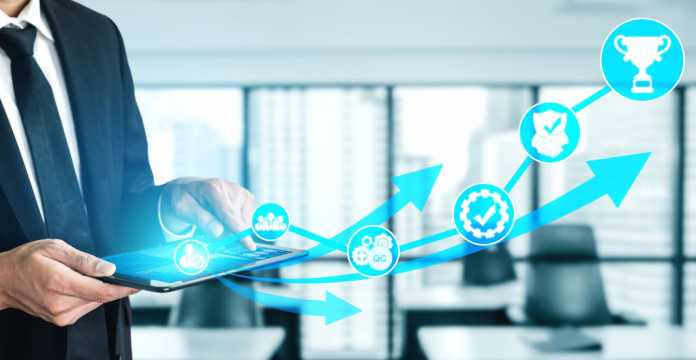
Table of Contents:
- Introduction
- What is Quality Management
- Quality Management Team roles and responsibilities
- Various Job Roles of a Quality Team
- Conclusion
Introduction
The quality of products and services can make or break a company’s reputation. Ensuring excellence is no longer just an option—it’s a necessity. This is where the quality management team plays a pivotal role in maintaining high standards and driving continuous improvement. In this blog, we will discuss the quality management team’s roles and responsibilities.
We will explore how their strategic oversight, attention to detail, and commitment to best practices help organizations achieve and sustain superior quality. From establishing vital quality control processes to fostering a culture of continuous improvement, these efforts are essential for maintaining high standards.
What is Quality Management?
Quality management is a comprehensive approach focused on ensuring that an organization’s products or services consistently meet or exceed customer expectations. It encompasses all activities and tasks necessary to maintain a desired level of excellence, including determining a quality policy, creating and implementing quality planning and assurance, quality control, and quality improvement. Quality management is structured around four components:
- Quality Planning: Identifying which quality standards are relevant to the project and determining how to satisfy them
- Quality Assurance: The systematic activities implemented within the quality system to provide confidence that a product or service will fulfill quality requirements
- Quality Control: The operational techniques and activities used to fulfill quality requirements, including the monitoring and recording results to evaluate the performance
- Quality Improvement: Ongoing efforts to enhance product quality, service quality, and process efficiency
Quality management aims to ensure that all the organization’s stakeholders work collectively to change the company’s rules, products, services, and experience to deliver the long-term benefit that arises from client happiness.
Quality Management Team Roles and Responsibilities
A Quality Management Team (QMT) is essential in any organization aiming to deliver high-quality products or services. This team is responsible for implementing, maintaining, and improving quality management systems (QMS). Here are the quality team roles and responsibilities typically associated with:
- Developing Quality Policies and Objectives: Establish clear quality policies and set measurable quality objectives that align with the organization’s goals
- Implementing Quality Management Systems: Ensure that the QMS is effectively implemented across all departments and processes
- Conducting Training and Awareness Programs: Educate employees about quality standards, procedures, and their roles in maintaining quality
- Performing Audits and Inspections: Regularly conduct internal audits and inspections to ensure compliance with QMS
- Managing Non-Conformances: Identify, document, and take corrective actions for any non-conforming products or processes
- Facilitating Continuous Improvement: Promote a culture of continuous improvement by identifying areas for improvement and implementing changes
- Ensuring Regulatory Compliance: Stay up-to-date with industry regulations and ensure the organization’s compliance
- Communicating with Stakeholders: Maintain clear and effective communication with internal and external stakeholders regarding quality issues and improvements
- Reporting on Quality Performance: Provide regular reports on the performance of the QMS to top management and other stakeholders
- Customer Satisfaction: Ensure customer satisfaction by addressing complaints and incorporating customer feedback into quality improvement initiatives
Now, we have a brief overview of quality team roles and responsibilities. We will discuss the roles of a quality team.
Various Job Roles of a Quality Team
A Quality management team ensures that products and services meet specified standards and customer expectations. Here are various job roles typically found within a Quality Team:
Quality Team Leader
Quality team leader responsible for managing the quality team, setting goals, and ensuring that quality objectives are met. The following are the responsibilities of a quality team leader:
- Provide direction and support to the quality team, ensuring alignment with organizational goals
- Coordinate activities across different quality functions, such as quality control, quality assurance, and quality improvement
- Monitor team performance, provide feedback, and implement improvement plans
- Address and resolve quality-related issues and escalate significant problems to senior management
- Facilitate communication within the team and with other departments to ensure a unified approach to quality management
Mastering quality function deployment is essential for a quality team leader. Choose a comprehensive QFD Training Course to enhance your leadership capabilities and ensure top-quality results.
Quality Team Members
Quality team members carry out specific tasks related to quality control, assurance, and improvement, supporting the overall quality management system. The following are the responsibilities of a quality team member:
- Conduct inspections and tests to ensure products or processes meet quality standards
- Collect and analyze quality data to identify trends and issues
- Maintain accurate records of inspections, tests, and quality issues
- Assist in the implementation of quality initiatives and improvements
- Participate in training programs to stay updated on quality standards and procedures
Lead Auditor
The lead auditor is responsible for planning, conducting, and reporting on internal and external quality audits. The following are the responsibilities of a lead auditor:
- Develop audit plans, including scope, objectives, and criteria
- Lead audit teams in conducting audits, ensuring thorough examination of processes and compliance with standards
- Document and report audit findings, including non-conformances and areas for improvement
- Ensure that corrective actions are implemented and verified
- Train and mentor junior auditors and quality team members on audit processes and best practices
Prepare yourself for the challenges of a Lead Auditor role with Lean IT Foundation Certification Training. Gain the skills to implement lean practices and improve audit outcomes effectively.
Quality Assurance Manager
The Quality Assurance (QA) Manager oversees the quality assurance processes and ensures that products and services meet established quality standards. The following are the responsibilities of a QA manager:
- Develop, implement, and maintain the quality management system (QMS)
- Ensure compliance with industry standards, regulations, and customer requirements
- Identify opportunities for process improvement and lead initiatives to enhance quality
- Provide training on quality standards, procedures, and best practices to employees
- Report on QA activities, performance metrics, and improvements to senior management
Audit Team
The audit team conducts internal and external audits to assess compliance with quality management systems and standards. The following are the responsibilities of an audit team:
- Prepare for audits by reviewing relevant documentation and standards
- Perform audits, including interviews, document reviews, and process observations
- Record audit findings, including any non-conformances, observations, and areas for improvement
- Compile audit reports and present findings to management
- Work with relevant departments to develop and implement corrective actions based on audit findings
- Conduct follow-up audits to ensure that corrective actions have been implemented and are effective
Conclusion
A Quality management team plays a crucial role in ensuring that an organization’s products, services, and processes meet the highest standards of quality and compliance. By planning, implementing, monitoring, and continually improving quality management systems, the team fosters a culture of excellence and customer satisfaction. Their responsibilities span from developing quality policies and conducting audits to managing non-conformances and facilitating training, all of which contribute to the organization’s overall success and competitive edge in the market. Effective quality management protects the organization’s reputation and drives operational efficiency and innovation.
Understand the key roles and responsibilities of a quality team with our specialized Six Sigma and Quality Management Certification Courses. Gain the skills needed to lead your team to success. Get certified and lead the way!