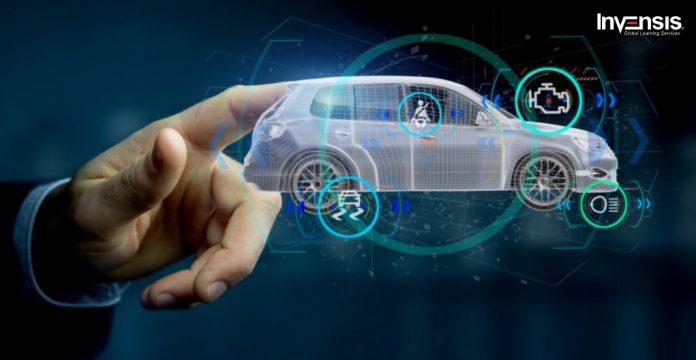
Six Sigma is a quality management methodology aiming to improve product and service quality by identifying and eliminating defects. It is used in the automotive industry to improve the quality of vehicles and manufacturing processes, reduce costs, and increase efficiency. It is a data-driven approach that uses statistical tools and techniques to identify and eliminate sources of variation and improve performance. Six Sigma can be applied to various aspects of the automotive industry, such as design, engineering, production, and service.
So, in this blog, let us learn how six sigma can be implemented in the automotive industry.
How can Six Sigma Be Applied to the Automotive Industry?
Six Sigma can be applied to various aspects of the automotive industry, such as design, engineering, production, and service. Some specific examples of how Six Sigma can be applied in the automotive industry include:
Design
Six Sigma can be used to improve vehicles’ design by identifying and eliminating defects that may cause problems during production or use. This can be done by using statistical tools and techniques to analyze data on customer complaints and warranty claims and using this information to identify and address the root causes of defects.
Engineering
Six Sigma can be used to improve the engineering of vehicles by identifying and eliminating defects in the manufacturing process. This can be done by using statistical tools and techniques to analyze data on production defects and using this information to identify and address the root causes of defects.
Production
Six Sigma can improve vehicles’ production by identifying and eliminating defects in the manufacturing process. This can be done by using statistical tools and techniques to analyze data on production defects and using this information to identify and address the root causes of defects.
Service
Six Sigma can be used to improve the service of vehicles by identifying and eliminating defects in the service process. This can be done by using statistical tools and techniques to analyze data on service defects and using this information to identify and address the root causes of defects.
Overall Six Sigma can be used to improve the quality of vehicles and manufacturing processes, reduce costs, and increase efficiency in the automotive industry. It is a data-driven approach that uses statistical tools and techniques to identify and eliminate sources of variation and improve performance.
Benefits of Six Sigma in the Automotive Industry
There are several benefits of implementing Six Sigma in the automotive industry:
Improved Quality
Six Sigma helps improve vehicles’ quality by identifying and eliminating defects in the design, engineering, production, and service processes. This can lead to fewer warranty claims and customer complaints, resulting in cost savings and improved customer satisfaction.
Reduced Costs
Six Sigma helps to reduce costs by identifying and eliminating inefficiencies in the manufacturing process. This can lead to lower production costs, resulting in increased profitability.
Increased Efficiency
Six Sigma helps to increase efficiency by identifying and eliminating bottlenecks in the manufacturing process. This can lead to shorter production times and improved production flow, resulting in increased productivity and improved on-time delivery.
Better Product Design
Six Sigma helps improve vehicles’ design by identifying and eliminating defects that may cause problems during production or use. This can lead to better-designed vehicles that are more reliable and require less maintenance, resulting in lower costs and improved customer satisfaction.
Improved Employee Engagement
Six Sigma helps to improve employee engagement by involving them in identifying and eliminating defects. This can lead to a more motivated workforce and improved employee satisfaction.
Continual Improvement
Six Sigma is a continuous improvement method, which means that it is not a one-time project but an ongoing effort. This can lead to long-term benefits for the automotive industry, such as improved quality, reduced costs, and increased efficiency.
Overall, the benefits of Six Sigma in the automotive industry include improved quality, reduced costs, increased efficiency, better product design, improved employee engagement, and a focus on continual improvement. In addition, by implementing Six Sigma, automotive companies can improve their bottom line and increase customer satisfaction.
Examples of Successful Six Sigma Implementation in the Automotive Industry
There are several examples of successful Six Sigma implementation in the automotive industry:
General Motors
General Motors (GM) was one of the first companies to adopt Six Sigma, starting in the late 1980s. GM used Six Sigma to improve the quality of its vehicles, reduce costs, and increase efficiency. As a result, GM was able to reduce warranty costs by $2 billion and improve customer satisfaction.
Volkswagen AG
Volkswagen AG adopted Six Sigma in the 2000s and used it to improve the quality of its vehicles and reduce costs. Volkswagen used Six Sigma to improve the design of its vehicles, reduce production defects, and improve the efficiency of its manufacturing processes. As a result, Volkswagen reduced warranty costs and improved customer satisfaction.
The above 2 examples demonstrate the effectiveness of Six Sigma in the automotive industry. By using Six Sigma, companies such as General Motors, Ford, Toyota, Honda, and Volkswagen were able to improve the quality of their vehicles, reduce costs, and increase efficiency.
Challenges for Six Sigma Implementation in the Automotive Industry
There are several challenges and considerations for implementing Six Sigma in the automotive industry, including:
- Complex supply chain: The automotive industry has a complex global supply chain, making implementing and maintaining Six Sigma processes difficult.
- High variability in product design: Automotive products are highly customized and have a lot of design variability, making it difficult to standardize processes and implement Six Sigma tools.
- Quality concerns: The automotive industry is heavily regulated, and quality is of paramount concern. Six Sigma implementation must be done in a way that does not compromise quality.
- Resistance to change: Some employees may resist change and need to be more comfortable with Six Sigma’s new processes and tools.
- High costs: Implementing Six Sigma can be expensive and requires significant investment in training, process improvement, and quality control.
- Long-term commitment: Six Sigma is a long-term commitment requiring ongoing investment and management support to succeed.
- Data collection and analysis: Automotive industry is data-intensive, so implementing six Sigma may require a significant amount of data collection, analysis, and management.
- Cross-functional collaboration: Six sigma implementation requires collaboration across different departments and functions, and building and maintaining that level of collaboration may be challenging.
Tools and Techniques Used in Six Sigma for the Automotive Industry
DMAIC
DMAIC (Define, Measure, Analyze, Improve, Control) is a structured approach to improve existing processes and eliminate defects. It is a five-step process that helps identify and remove the root cause of a problem.
The five steps are:
- Define: Identify the problem and define the project goals and objectives.
- Measure: Gather and analyze data to understand the current performance of the process.
- Analyze: Identify the root cause of the problem by using tools such as fishbone diagrams, Pareto charts, and cause-and-effect diagrams.
- Improve: Develop and implement solutions to address the root cause of the problem.
- Control: Establish controls to maintain the improvements made and prevent the problem from recurring.
DMAIC (Define, Measure, Analyze, Improve, Control) process was used by a major automotive manufacturer to improve the efficiency of their assembly line, resulting in a significant reduction in defects and increased production output.
Statistical Process Control (SPC)
SPC is a method used to monitor and control processes by analyzing and controlling process variables to ensure they are within acceptable limits. It involves collecting data on the process, creating control charts, and identifying patterns or trends in the data. Tools used in SPC include control charts, histograms, Pareto charts, and scatter plots. SPC helps identify process variations early and helps to take corrective action before defects occur.
A supplier to a major automotive company used statistical process control (SPC) to monitor and control the quality of their parts, resulting in a significant reduction in defects and improved customer satisfaction.
Design of Experiments (DOE)
DOE is a structured approach used to optimize process parameters and product design by systematically varying inputs and measuring outputs. It helps identify the relationship between inputs and outputs and helps determine the optimal conditions for a process. DOE uses tools such as full factorial designs, fractional factorial designs, and response surface methodology to optimize the process. This can be used in the automotive industry to optimize the design of new car models, production processes, and materials used.
A major automotive company used a design of experiments (DOE) to optimize the design of a new vehicle component, resulting in improved performance and reduced development costs.
Failure Modes and Effects Analysis (FMEA)
It is a structured approach to identifying potential failure modes and the effects of these failures on the system. It is used to prioritize the potential failure modes based on their likelihood of occurrence and the potential impact on the customer. This method is used in the automotive industry to identify potential failure modes in vehicles’ design and production process.
A major automotive company used failure mode and effects analysis (FMEA) to identify potential failure modes in a new vehicle model, resulting in improved reliability and reduced warranty costs.
Value Stream Mapping
Value stream mapping (VSM) is used to analyze and optimize the flow of materials and information in a manufacturing process. It identifies and eliminates waste in the process, such as excess inventory, unnecessary steps, and delays. VSM can be used in the automotive industry to optimize the flow of materials and information throughout the supply chain and production process.
A manufacturing plant of a major automotive company used value stream mapping (VSM) to identify and eliminate waste in their production process, resulting in a significant increase in efficiency and cost savings.
Six Sigma project charter
A Six Sigma project charter is a document that outlines the scope, objectives, and key success factors of a Six Sigma project. It is used to define the problem, establish the project team and their roles, and provide a roadmap for the project. This document guides the project team throughout the DMAIC process and helps to ensure that the project stays on track.
Case Study
Case Study: Six Sigma Implementation at XYZ Automotive Plant
Background
XYZ Automotive is a leading manufacturer of vehicles in the United States, focusing on producing high-quality, reliable cars at competitive prices. However, the company has recently struggled to maintain its market share due to increasing competition and rising costs. As a result, XYZ Automotive decided to implement the Six Sigma methodology to improve efficiency and reduce costs at its main production plant.
Implementation
The Six Sigma implementation at XYZ Automotive began with the selection of a team of experts to lead the project. This team included experienced Six Sigma practitioners, engineers, and managers from various departments within the company. Together, they identified the key areas of the production process that were causing the most problems and set out to improve them.
The first step was to define the project objectives and establish measurable targets for improvement. This included reducing the number of defects in the production process, increasing the efficiency of the assembly line, and reducing the overall cost of production.
Next, the team collected and analyzed data on the production process, using statistical tools such as statistical process control (SPC) and design of experiments (DOE) to identify the root causes of problems. Based on this analysis, the team developed and implemented a series of improvements to the production process, including changes to the assembly line layout, introduction of new technologies, and the implementation of new quality control procedures.
Results
The Six Sigma implementation at XYZ Automotive was a success, resulting in significant improvements in efficiency, quality, and cost. In particular, the number of defects in the production process was reduced by 60%, the efficiency of the assembly line was increased by 30%, and the overall cost of production was reduced by 20%. Additionally, employee satisfaction and morale improved significantly due to the increased involvement of employees in the improvement process.
Conclusion
The Six Sigma methodology effectively improved efficiency and reduced costs at XYZ Automotive. By focusing on the key areas of the production process and utilizing statistical tools to identify and solve problems, the company achieved significant improvements in quality and efficiency, ultimately helping to increase its competitiveness in the automotive market.
The Future Outlook for Six Sigma in the Automotive Industry
The Six Sigma methodology has been widely adopted in the automotive industry to improve quality and efficiency in manufacturing. Its focus on data-driven problem-solving and continuous improvement aligns well with the industry’s need for precision and efficiency. As a result, six Sigma is expected to continue to be a key tool for the automotive industry as companies look to improve their operations and remain competitive. Additionally, Six Sigma will help the industry to adapt to new technologies such as electric vehicles, autonomous driving, and connected cars.
Conclusion
Six Sigma is a powerful tool used effectively in the automotive industry to improve quality and reduce costs. By using data-driven methods to identify and eliminate defects, Six Sigma can help companies optimize their processes and increase efficiency. As the automotive industry continues to evolve and adapt to new technologies and changing consumer demands, Six Sigma will be an important tool for companies to stay competitive and ensure customer satisfaction.
Want to know more about six sigma? Then, take up our various six sigma related courses like Six Sigma Green Belt Certification, Six Sigma Black Belt Certification, and Six Sigma Yellow Belt Certification and stand out of the crowd.
Glossary
- Six Sigma: A methodology for process improvement that aims to reduce defects and variability in a process to a rate of 3.4 defects per million opportunities. Six Sigma uses statistical tools and techniques to measure and improve the quality of a process.
- Automotive Industry: The industry involved in the design, development, production, and sale of vehicles, including cars, trucks, buses, and motorcycles.
- DMAIC: A Six Sigma methodology for defining, measuring, Analyzing, Improving, and Controlling. It is used to improve an existing process by identifying and removing the causes of defects and variability.
- Value Stream Mapping: A tool used in Lean manufacturing to identify and eliminate waste in a process. It maps the flow of materials and information in a process and identifies areas where improvements can be made.
- Statistical Process Control (SPC): A method of monitoring a process using statistical tools and techniques to ensure that the process is in Control and producing products that meet specifications. SPC is often used in the automotive industry to monitor the quality of manufactured parts and detect any issues early.
- Green Belt: A Six Sigma certification that indicates a basic understanding of the Six Sigma methodology. Green Belts are typically responsible for leading small Six Sigma projects and assisting Black Belts on larger projects.
- Black Belt: A Six Sigma certification indicates a higher understanding of the Six Sigma methodology and experience leading Six Sigma projects. Black Belts are typically responsible for leading large Six Sigma projects and training and mentoring Green Belts.
———————————————————————————————————————————-Organize Corporate Group Six Sigma Green Bet Certification training for your teams around the world
Invensis learning provides In-person and live virtual instructor-led corporate training program customized for enterprise teams who wish to train their employees on specific aspects of their job processes or responsibilities. The corporate training by our expert certified trainers will enhance your learning curve and enable your teams to utilize their skills to meet industry standards.
- Experienced & Industry Specific Trainers
- Lifetime LMS access
- Deliver sessions across continents via In-Person/ Virtual Instructor-Led Training
- Customized Training
———————————————————————————————————————————-