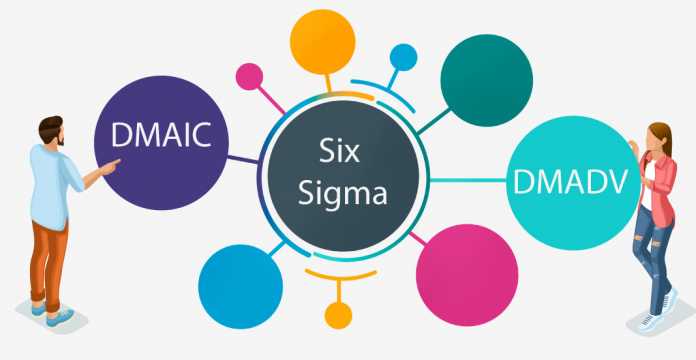
In today’s cut-throat competition world, every organization is looking for a way to get maximum output and productivity at minimal costs. One methodology that has been around for decades and has proved its worth time and again is Six Sigma. In fact, according to the 6Sigma Academy, Black Belts save companies approximately $230,000 per project and can complete more than 4-6 projects a year.
That being said, while the importance of Six Sigma can’t be overstated, companies do need to choose from an idea framework for their companies from Six Sigma’s DMAIC and DMADV.
Lean Six Sigma Green Belt practice regularly concentrates on the Six Sigma framework of DMAIC, which is mainly designed for developing existing processes. But what happens if a process needs to be redesigned in order to make an improvement? While it is not often considered in compact Six Sigma practice, there is a different Six Sigma approach – DMADV – which refers to situations where a process must be redesigned for improvement.
In this article, we will discuss what DMADV is all about and how is it different from DMAIC.
What Is DMADV?
Starting with DMAIC, the term is essentially an acronym for Define, Measure, Analyze, Improve and Control. On the other hand, when it comes to DMADV, the first three letters of this structure are identical to DMAIC and stand for Define, Measure and Analyze sequentially. However, the last two letters stand for Design and Verify.
The DMADV Framework
Each aspect of the DMADV framework follows these agendas:
- Determine consumer demands and intentions for the process, product, or service
- Measure and analog performance to consumer requirements
- Analyze and evaluate the design for the process, product, or service
- Design and execute the pattern of new methods needed for the new process, product, or service
- Check effects and maintain performance
The primary difference between DMAIC and DMADV frameworks is, that DMAIC will be practiced when you are seeking to enhance or develop a process that is now into the present.
The DMADV (Define-Measure- Analyze-Design- Verify) method intends to redesign a questionable process or product. The path initially follows the first three levels of DMAIC. It then varies in the last two steps by including the Design / Redesign and Verify or Validate levels to gain the changes needed. This method prevents difficulties from following through with quality and sturdy design ideas.
Design
In the initial phase, goals are classified into the purpose of the project. During this grade, practical and measurable goals are set that are related to both the organization and its stakeholders. After the objects have been set, a clear scope must be set for the project, and a clear strategy must be followed with each of the project aims that will satisfy the expectations of the organization and the patrons.
Measure
The next step in DMADV is Measuring. At this level, the parts that are important to quality should be measured. It’s essential to define the specifications of the metrics. How the metrics will be measured must be well-designed to present useful results. It must value quality, risk, process capability, and product capability, among others.
Analyze
While the Analyze phase of DMADV, several actions must be practiced. These involve developing design options, defining the optimal blend of requirements to produce value within the given limitations, conceptual designs, knowing the best parts, and then developing the best plan. Here, the total lifecycle cost of the model is determined. During the analysis phase, we must ask ourselves – everything is the best design that will assist us in meeting our goals?
Develop
The fourth step of DMADV includes a high level and a full design for the design that was chosen in the early phase. Each element of the model has selected a priority after which a high-level plan is developed. After a high-level design has been received, a more detailed design will be constructed as a model. Here, any mistakes which may occur can be identified, and the new process design can be changed to avoid mistakes.
Verify
Now, in the last stage of DMADV, it is time for the unit to verify whether the plan is adequate. Can the design be practiced in the real world? Guide studies will need to be conducted as well as production-scale studies. Here it is essential to ensure that the entire best quality possible can be obtained. That is, after all the whole point. The Verify step of DMADV also involves an implementation plan that specifies how the new method will transition into routine operation.
The Difference Between DMADV and DMAIC
Let’s glance at some more differences between DMADV and DMAIC.
- DMAIC focuses on reducing variation in an actual process while DMADV is about creating a process that is “first time right:”
- DMAIC is all about changing while DMADV is a bar
- DMAIC practices quantitative analytical tools while DMADV uses qualitative media
- DMAIC concentrates on the critical few QTC parameters while DMADV focuses on all of them
- DMAIC is usually a shorter-term project than DMADV, which is more long-term.
It is essential to note that Six Sigma is not restricted to a specific kind of process or query. While most cases given are from a manufacturing background, Six Sigma can be implemented to improve any process in any environment. It is also not restricted to enhancing an existing process but can be applied to design entirely new processes as we have discussed in this article. DMADV is a helpful way to use Six Sigma to think outside of the box and to fully redesign processes that cannot be improved using the DMAIC method.
Conclusion
As Six Sigma proceeds to develop and address 21st-century business concerns and purposes, professionals that show knowledge of these methods could find many suitable opportunities in a variety of industry backgrounds. At Invensis Learning, you can learn more about the Green Belt, Black Belt, and Yellow Belt in Six Sigma and how they can be beneficial for any organization.