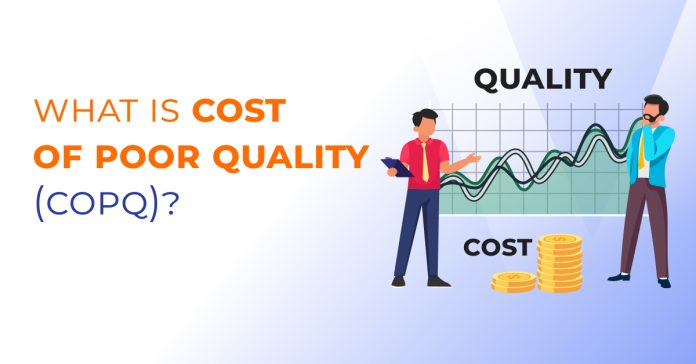
Have you ever considered the hidden costs associated with products or services that don’t quite meet the mark? We’re not just talking about frustrated customers and bad reviews. Businesses can face a surprising financial burden due to poor quality.
This cost is known as the Cost of Poor Quality (COPQ), and understanding it can be a game-changer for your organization.
This blog post explores the world of COPQ, providing a comprehensive definition and exploring its various aspects.
We’ll uncover the different categories of COPQ and the hidden costs they represent. By the end, you’ll gain valuable insights into how prioritizing quality can save your business money and boost customer satisfaction.
Table of Contents
- What is the Cost of Poor Quality?
- What are the Categories of Cost of Poor Quality?
- Why Cost of Poor Quality?
- When to Use the Cost of Poor Quality?
- Cost of Quality and Organizational Objectives
- Conclusion
What is the Cost of Poor Quality?
The cost of Poor Quality (COPQ) refers to an organization’s financial and non-financial costs associated with producing defective or substandard products or services. It measures the expenses of failing to meet quality standards and the additional resources required to correct defects, address customer complaints, and rectify issues in processes or products.
COPQ contains visible and hidden costs throughout the product or service lifecycle, including design, production, distribution, and customer service.
These costs can significantly impact an organization’s profitability, operational efficiency, customer satisfaction, and overall competitiveness in the marketplace.
By understanding and managing COPQ effectively, organizations can identify the sources of poor quality, implement corrective actions, and improve their quality management system practices to reduce costs, enhance product or service quality, and drive business growth.
What are the Categories of Cost of Poor Quality?
The Cost of Poor Quality (COPQ) types help to classify and understand the different types of costs that arise due to poor quality in products or services. These categories provide a structured approach to identifying and measuring the financial and non-financial impacts of quality issues within an organization.
The four main categories of COPQ are:
-
Prevention Costs
Definition: These are proactive investments a company makes to control quality issues from arising in the first place
Examples:
- Employee training and development programs focused on quality awareness, best practices, and continuous improvement
- Quality planning activities, including risk assessment, process design, and implementation of quality management systems
Impact:
Investing in prevention activities can cause significant long-term benefits by reducing the likelihood of defects, enhancing process efficiency, and improving overall product or service quality.
By proactively addressing potential quality issues and implementing preventive measures, organizations can minimize internal and external failure costs, enhance customer satisfaction, and strengthen their competitive position in the marketplace.
-
Appraisal Costs
Definition: These are the costs associated with activities that ensure products or services meet quality standards
Examples:
- Inspection and testing activities carried out during various stages of production or service delivery
- Quality audits conducted to assess compliance with organizational and regulatory requirements
Impact:
While these costs are necessary to maintain and monitor quality levels, excessive appraisal costs may indicate inefficiencies in processes or inadequate quality management practices. Effective appraisal strategies can help organizations detect and address quality issues early, reducing internal and external failure costs
-
Internal Failure Costs
Definition: These are the financial losses incurred when defects are found before the product or service reaches the customer
Examples:
- Scrap and waste from defective products that cannot be repaired or sold
- Rework or corrective actions required to fix defects and bring products up to quality standards
Impact:
These costs directly impact the production process and can lead to decreased efficiency, increased production time, and higher operating expenses. They also reflect lost opportunities to generate revenue from defect-free products
-
External Failure Costs
Definition: These are costs incurred when defects are identified after the product has been delivered to the customer
Examples:
- Warranty claims and repairs or replacements for defective products returned by customers
- Costs associated with handling customer complaints, including customer service time and resources
Impact:
These costs can have a significant financial and reputational impact on organizations. They erode customer trust, lead to increased customer turnover, and may result in legal liabilities or regulatory fines, thereby affecting long-term profitability and competitiveness
Why Cost of Poor Quality?
Understanding and managing the Cost of Poor Quality (COPQ) is essential for organizations for several compelling reasons:
-
Financial Impact
COPQ can represent a significant portion of a company’s operating expenses. Estimates suggest it can range from 10-20% or even higher, directly impacting profitability. By minimizing COPQ, companies free up resources to invest in growth and innovation.
-
Customer Satisfaction
Poor quality directly translates to dissatisfied customers. Defects, malfunctions, and poor service lead to frustration, complaints, and, ultimately, lost business. Focusing on COPQ demonstrates a commitment to quality, fostering customer loyalty and repeat business.
-
Brand Reputation
A string of quality issues can severely damage a company’s brand image. Negative word-of-mouth spreads quickly, especially in today’s digital age. By prioritizing COPQ, businesses build trust and solidify their reputation for reliability.
-
Efficiency and Productivity
Addressing poor quality can lead to significant improvements in efficiency and productivity. Less rework, fewer errors, and streamlined processes translate to a smoother operation and a more productive workforce.
-
Continuous Improvement
Analyzing COPQ helps identify areas for improvement across the entire value chain. By understanding where quality issues arise, companies can implement targeted solutions and foster a culture of continuous improvement, leading to overall better performance.
When to Use Cost of Poor Quality?
The concept of Cost of Poor Quality (COPQ) is a valuable tool for businesses across various situations.
Here are some key moments to leverage COPQ:
-
Making the Case for Quality Initiatives
COPQ data can demonstrate the potential return on investment (ROI) when proposing investments in quality control measures, training, or new equipment. By highlighting the financial losses due to poor quality, you can make a strong case for prioritizing quality initiatives.
-
Identifying Areas for Improvement
COPQ analysis helps pinpoint areas where quality issues are most prevalent. For example, if you see a high cost of warranty claims, this indicates a potential problem with product durability. By analyzing COPQ data, you can identify weak spots in your production process and target them for improvement.
-
Evaluating the Effectiveness of Quality Programs
Once you’ve implemented quality improvement initiatives, COPQ can be used to track their effectiveness. By monitoring changes in COPQ over time, you can assess whether your programs reduce errors and save money.
-
Prioritizing Resources
Businesses often need more resources. COPQ analysis can help you allocate resources strategically. By identifying the categories of COPQ that are costing the most, you can focus your efforts on areas with the greatest potential for improvement.
-
Benchmarking Against Competitors
In some industries, COPQ data can be used to benchmark against competitors. This can provide valuable insights into industry standards and help you identify areas where your company can gain a competitive edge through superior quality.
Cost of Quality and Organizational Objectives
The costs associated with maintaining quality standards, implementing quality enhancements, and attaining objectives should be meticulously overseen to ensure that quality’s impact on the organization remains favorable.
These expenses should genuinely reflect the commitment to quality, and the most accurate way to gauge this is through a Cost of Quality analysis. Such an evaluation offers a structured approach to appraising the efficacy of quality management, pinpointing areas of concern, identifying opportunities for improvement and potential savings, and establishing action priorities.
Cost of Quality serves as a vital communication instrument. Philip Crosby emphasized its potency as a tool to heighten awareness regarding the significance of quality. He coined the term the “price of nonconformance,” contending that organizations essentially decide to bear the costs of subpar quality.
It’s not uncommon for organizations to witness quality-related expenses amounting to 15-20% of their sales revenue, with some even reaching up to 40% of overall operations. A commonly accepted benchmark suggests that the costs attributed to poor quality in a flourishing company could hover around 10-15% of operations. Implementing effective quality enhancement initiatives can substantially curtail these costs, directly bolstering profits.
Once the Cost of Quality framework is firmly in place, it should evolve dynamically, exerting a beneficial influence on the organization’s mission fulfillment, goal attainment, and overarching objectives.
Conclusion
The Cost of Poor Quality (COPQ) is a critical concept for any organization striving for success. It goes beyond simply fixing mistakes; it encompasses the financial burden of producing or delivering subpar products or services. By understanding the different categories of COP – businesses can identify areas for improvement and make strategic investments in quality.
Focusing on COPQ isn’t just about saving money. It’s about building a strong foundation for long-term growth. By prioritizing quality, businesses can deliver a better product or service, build stronger customer relationships, and achieve sustainable profitability. Remember, COPQ is a powerful tool to analyze, improve, and achieve excellence in everything you do.
Mastering the Cost of Poor Quality is just the beginning. Take it to the next level with Invensis Learning’s Quality Management Certification Courses. Reduce waste, boost efficiency, and delight customers. Our programs equip you with the skills to achieve operational excellence.