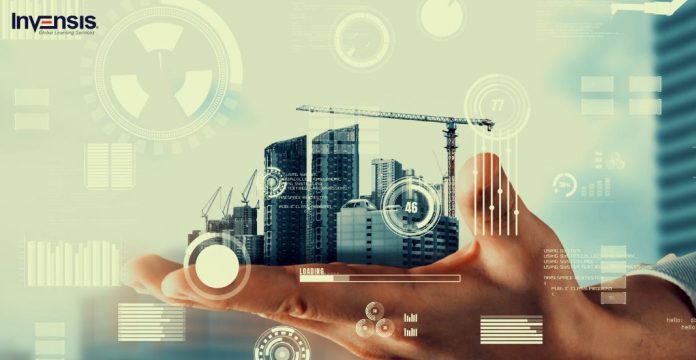
The construction industry is known for its complex processes and high level of variability, which can lead to inefficiencies and errors. Using the Six Sigma methodology, we can identify and eliminate these issues to improve the quality of the end product and increase the overall efficiency of the process.
In this blog, we will explore the key performance indicators crucial in the construction industry and how Six Sigma can be used to improve them. We will also look at real-world case studies of successful Six Sigma implementations in construction companies and provide an overview of the methodology and its benefits.
Overview of the Construction Industry and its Challenges
The construction industry involves building, maintaining, and repairing structures such as roads, bridges, buildings, and other infrastructure. It is a broad field encompassing many different trades and specialties, including electrical work, plumbing, carpentry, and masonry. The industry employs many workers and significantly contributes to a country’s economy.
Construction projects can range from small renovations to large-scale, multi-billion dollar developments and can be funded by private individuals, businesses, or government agencies. The industry is also subject to various regulations and building codes to meet safety and quality standards.
The Challenges of the Construction Industry and How Does Six Sigma overcomes It?
Challenges of the Construction Industry | How Can Six Sigma Overcome These Challenges? |
Labor Shortages | Improve efficiency and productivity to reduce the reliance on labor |
Rising Costs | Identify and eliminate waste to reduce costs associated with materials, labor, and equipment |
Schedule Delays | Improve schedule predictability by identifying and mitigating factors that contribute to delays |
Safety Concerns | Improve safety by identifying and eliminating hazards on construction sites and improving safety procedures |
Environmental Impact | Use Six Sigma tools to identify and implement sustainable materials and methods that minimize the environmental impact |
Complexity and Advancements | Simplify construction processes and make them more efficient and predictable |
Bureaucracy and regulations | Streamline the process of complying with regulations and reduce the time and cost associated with bureaucracy |
Time and Budget Constraints | Improve project management by better-managing budgets and schedules and improving communication and collaboration among project stakeholders. |
Building a data-driven culture | Encourage data collection, and with the help of statistical tools, use it to make informed decisions and track progress. |
Identifying Key Performance Indicators (KPIs) in the Construction Industry
Key Performance Indicators (KPIs) are metrics used to measure the performance of a business or organization. For example, in the construction industry, KPIs can be used to measure the performance of construction projects and companies. Some examples of KPIs in the construction industry include:
- Schedule Performance: This KPI measures the progress of a construction project against the project schedule. It is typically measured as a percentage of planned vs. actual progress.
- Cost Performance: This KPI measures the progress of a construction project against the project budget. It is typically measured as a percentage of planned vs. actual costs.
- Safety Performance: This KPI measures the safety performance of a construction company or project. It is typically measured as the number of incidents or accidents per a set period.
- Quality Performance: This KPI measures the quality of a construction project or company. It is typically measured as the number of defects or rework required per a set period.
- Productivity Performance: This KPI measures the productivity of a construction company or project. It is typically measured as the amount of work completed per a set period.
- Equipment Utilization: This KPI measures equipment utilization on a construction project. It is typically measured as a percentage of planned vs. actual usage.
- Labor Utilization: This KPI measures labor utilization on a construction project. It is typically measured as a percentage of planned vs. actual usage.
- Environmental Impact: This KPI measures the environmental impact of a construction project. It is typically measured as a percentage of waste material recycled or reused or the number of trees planted per a set period.
How Does Six Sigma Help in Improving Construction KPIs?
Six Sigma is a methodology that utilizes statistical tools and techniques to identify and eliminate defects and reduce process variability. In the construction industry, it can be used to improve key performance indicators (KPIs) such as cost, schedule, safety, and quality. By using Six Sigma to identify and eliminate inefficiencies, construction organizations can reduce costs, improve project schedules, and ensure that projects are delivered on time and within budget while also ensuring a higher level of quality and safety. Six Sigma can also improve communication and collaboration between project stakeholders, which can further improve the overall performance of construction projects.
DMAIC in Construction
Defining and Measuring Process Performance in Construction
Process performance in construction refers to the effectiveness and efficiency with which a construction project is planned, executed, and completed. It is an important aspect of construction management as it determines the success of a project in terms of cost, time, and quality.
Measuring process performance in construction involves assessing the following key areas:
- Project Completion Time: This metric measures how long it takes to complete a construction project from start to finish. It is important to ensure the project is completed on schedule to avoid delays and additional costs.
- Cost: One of the most important aspects of process performance is the project’s cost. This includes the initial budget and any additional costs incurred during the project. It’s important to keep the cost as close as possible to the original budget to achieve a profitable outcome.
- Quality: The quality of the final product is also an important aspect of process performance. This includes the quality of artistry and materials used and compliance with industry standards and regulations.
- Safety: Construction projects can be dangerous, and it is important to ensure that the work is carried out safely. This includes monitoring and reporting on safety incidents and implementing safety procedures and training.
- Adherence to Regulations: Construction projects must comply with various regulations and standards. These include building codes, environmental regulations, and health and safety laws. Measuring compliance with these regulations is an important aspect of process performance.
- Customer satisfaction: The satisfaction of the client or owner of the project is an important aspect of process performance, as it determines the project’s overall success. The client’s satisfaction can be measured by feedback and reviews after the completion of the project.
To improve process performance, construction organizations can implement best practices such as project management methodologies, use of technology, and effective communication and collaboration among team members. Additionally, regular monitoring and analysis of the key performance metrics can help identify areas for improvement and inform decision-making.
Analyzing data and identifying Root Causes of Defects in Construction
Analyzing data and identifying the root causes of construction defects is an important aspect of quality control and process improvement. The following steps can be taken to analyze data and identify the root causes of defects:
- Collect Data: The first step is collecting data on the construction project’s defects. This can include information such as the location of the defect, the type of defect, and the date and time it was discovered.
- Analyze the Data: Once the data has been collected, it should be analyzed to identify patterns and trends. This can include identifying the most common types of defects, the locations where they occur, and the times of day or week when they are most likely to occur.
- Identify Root Causes: After analyzing the data, the next step is identifying the defects’ root causes. This can be done using tools such as fishbone diagrams, cause and effect diagrams, or fault tree analysis. These tools help identify the defects’ underlying causes rather than just the symptoms.
- Implement Solutions: Once the root causes have been identified, solutions can be implemented to prevent the defects from recurring. These solutions can include changes to the design, materials, or processes used on the construction project.
- Monitoring: Regular monitoring is important to ensure that the solutions implemented effectively prevent defects. Data should be collected and analyzed again to ensure that the defects have been reduced or eliminated.
It’s important to note that root cause analysis is a continuous process and should be done regularly to ensure that the project quality standards are met. Additionally, involving all stakeholders in the process and encouraging them to report any defects they come across can also assist in identifying and preventing defects from occurring.
Implementing Solutions to Improve Process Performance in Construction
Implementing solutions to improve process performance in construction is an important aspect of construction management. Once the root causes of defects and issues have been identified through data analysis, the following steps can be taken to implement solutions:
- Develop a plan: Develop a plan that outlines the steps that will be taken to address the identified issues. This plan should include specific objectives, timelines, and resources to implement the solutions.
- Communication: Communicate the plan to all stakeholders, including team members, project managers, and clients. This ensures that everyone is aware of the issues and the steps being taken to address them.
- Training: Provide training and education to team members on the new processes, procedures, or technologies that will be implemented. This ensures that everyone can effectively implement the solutions.
- Implementation: Implement the solutions in a systematic and phased approach. This allows for testing and monitoring of the solutions to ensure they are effective and efficient.
- Monitoring and Evaluation: Regularly monitor and evaluate the solutions to ensure they achieve the desired results. Identify any additional issues that arise and take steps to address them.
- Continuous improvement: Regularly review and update the solutions to ensure they are still effective and efficient. Continuously improve the process to meet the organization’s goals and objectives.
- Technology adoption: Utilize technology to improve process performance. For example, using BIM (Building Information Modelling) can improve the process performance by reducing the project’s time and costs, improving the project’s quality and safety, and increasing the client’s overall satisfaction.
It’s important to note that implementing solutions to improve process performance is an ongoing process that requires commitment and resources from all stakeholders. Additionally, involving all stakeholders in the process and encouraging them to provide feedback on the solutions will help to ensure their success.
Monitoring and Controlling Process Performance to Maintain Improvements in Construction
Monitoring and controlling process performance involve regularly measuring and assessing the performance of a process, comparing it to established targets or standards, and taking corrective action if necessary to maintain or improve performance. This can include implementing process changes, training employees, or using data analysis to identify and address problem areas.
Continuous improvement techniques such as Six Sigma and Lean can also be used to systematically identify and eliminate sources of waste and inefficiency in the process.
Case Studies of Successful Six Sigma Implementations in the Construction Industry
There are several examples of successful Six Sigma implementations in the construction industry. Some notable examples include:
- Fluor Corporation: Fluor, a leading engineering, and construction company, implemented Six Sigma in 2001 and has since seen significant improvements in project quality, safety, and cost savings.
- Turner Construction: Turner Construction, one of the largest construction management firms in the United States, began implementing Six Sigma in 2004 and has since seen improvements in project management, resource allocation, and cost control.
- Whiting-Turner Contracting Company: Whiting-Turner, a leading construction management, and general contracting firm, implemented Six Sigma in 2005 and has since seen improvements in safety, quality, and cost savings.
- Bechtel: Bechtel, a global engineering, construction, and project management company, implemented Six Sigma in 2002 and has since seen improvements in project management, safety, and cost savings.
- Skanska: Skanska, one of the world’s leading project development and construction groups, implemented Six Sigma in 2000 and has seen improvements in cost savings, schedule adherence, and safety.
Six Sigma implementation can be tailored to specific industries, so these cases may not be the same as another construction company would experience. However, it gives an idea of the potential benefits of Six Sigma.
Conclusion
Six Sigma is a methodology that has been successfully implemented in various industries, including the construction industry. Using Six Sigma in construction can lead to significant improvements in project quality, safety, cost savings, and schedule adherence. Companies such as Fluor, Turner Construction, etc., have implemented Six Sigma and have seen positive results. In addition, the Six Sigma methodology can be tailored to the specific needs of a construction company, making it a versatile tool for improving operations and increasing efficiency.
Want to know more about six sigma? Then, take up our various six sigma related courses like the Six Sigma Green Belt Course, Six Sigma Black Belt Certification, and Six Sigma Yellow Belt Certification Training and stand out of the crowd.
Glossary
- Six Sigma: A methodology for process improvement that aims to reduce defects and increase efficiency. It is a data-driven approach that uses statistical methods to identify and eliminate sources of variability and improve process performance.
- Defects: Any nonconformance to a product or process specification. In construction, defects can include errors in design, materials selection, or issues with artistry.
- Process Improvement: Making changes to a process to make it more efficient, effective, or reliable. In construction, process improvement can include streamlining project management, improving resource allocation, or increasing safety.
- Safety: The state of being safe from harm or danger. In construction, safety refers to the measures taken to protect workers and others from accidents or injuries.
———————————————————————————————————————————-Organize Corporate Group Six Sigma Green Belt Certification training for your teams around the world
Invensis learning provides In-person and live virtual instructor-led corporate training program customized for enterprise teams who wish to train their employees on specific aspects of their job processes or responsibilities. The corporate training by our expert certified trainers will enhance your learning curve and enable your teams to utilize their skills to meet industry standards.
- Experienced & Industry Specific Trainers
- Lifetime LMS access
- Deliver sessions across continents via In-Person/ Virtual Instructor-Led Training
- Customized Training———————————————————————————————————————————