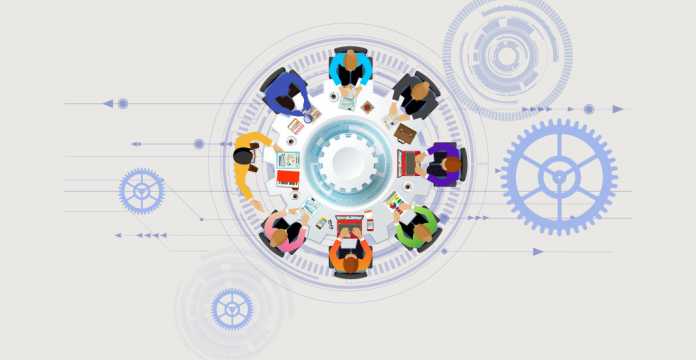
“Quality” is not just limited to some standardized values. It represents the extent to which a product or service matches the customer’s requirements.
Six Sigma’s deviations use a bell curve, which encourages the organization to tolerate only 3.4 defects per million steps. Therefore, with successful implementation, you can improve business processes like manufacturing, finance, human resources, projects, etc. It focuses on creating a “quality” output, one that leads to maximum customer satisfaction.
At its core, Six Sigma focuses on reducing “waste” using a combination of statistical and management tools. These tools help companies produce customer-friendly products and services.
Waste is any material or process which is more than what is required in the path to deliver the product or service. Since these unwanted materials or processes may only add to overall costs or time lag, it is imperative to minimize them.
This makes waste management a crucial aspect to consider if you want to maximize your company’s efficiency. Waste management essentially involves:
- Understanding the types of waste
- Know the rate at which the company can reduce the waste
- The necessary steps which the company needs to take
The DMAIC approach of Six Sigma is one of the popular methods to find the wastes or inefficiencies within your organization. This method focuses on replacing inefficiencies with innovative solutions to save you from unexpected disposal costs.
But first, you need to know your waste reduction rate.
What is your Waste Reduction Rate?
The waste reduction rate represents how well your company is adept at reducing the amount of waste.
You must know some perks of knowing the waste your company is generating. Understanding how waste is affecting your company helps you to:
- Identify the company’s disposal costs
- Calculate the extra time taken during a process
- Determine the margin by which the project exceeds the budget
- Identify the unnecessary inventory processes, and so on
The waste reduction rate gives you a clear idea of how well you have improved in terms of reducing them.
Mathematically waste reduction rate can be represented as:
Waste reduction rate=Wasted Raw Material in a particular period / Wasted Raw Material in the previous period x 100
Here you need to collect data from the previous year and the current period. You need to ensure that these data are from reliable sources and are accurate.
List of all Significant Wastes
For efficient waste management, you must understand the type of waste you are dealing with.
Six Sigma wastes are categorized into eight different types, namely:
Zero value Processes
Six Sigma focuses only on the process that adds value to product quality. When a step adds nothing significant to the process, you can consider it as “waste.”
It is easy to eliminate these steps from your process, and it will not affect the quality. Value Stream Mapping is one Six Sigma Tool, which can be used here. Analyzing all the steps helps to identify the areas which are only consuming time and money while delivering zero output to the entire process.
Over Production
When you produce goods more than what is required by the market trends, you are only wasting the resources and effort put into it. Six Sigma considers this as a waste as it involves unnecessary inventory carrying costs that add no significant value to the product’s quality.
To avoid this, you can use the Six Sigma tool known as “the pull system.” This tool encourages you to produce only when there is a demand in the market. This way, you can schedule and forecast production strategies and reduce unwanted inventory costs.
Motion
Any step in a process where there is unwanted motion creates a time lag, and it also costs the company transport charges.
An example can be a production engineer moving to and fro with his team to collect a few tools or documents. You can avoid unwanted motions if these are available within their reach.
The motion of this kind that adds to the cost and time is regarded as a Six Sigma waste.
Inventory
This waste is somewhat related to overproduction. When you overproduce, it directly adds to your storage and transportation expenses. Inventory wastes take up space and may sometimes require an extra workforce for safety and transportation needs. The storage needs of defective products that you cannot discard also come under this category.
As a manager, you can eliminate this waste by properly forecasting the needs and implementing a strict production process.
Transportation
Sometimes, due to an unplanned process, you may end up transporting a product unnecessarily. A classic example is delivering a product at the wrong address. Here due to inaccuracy in data, you had to ship and bear all the transportation costs that add nothing significant to the customer value.
Defects
Defects in products add to the inventory waste. Also, scrap or defective products degrade the company’s reliability among its customers. These are easy to find and define.
Unused Employee Talent
Any talent, if not used correctly and in time, is regarded as a waste. It happens mainly due to the lack of training facilities or motivating leadership in an organization.
Companies need to build a working culture where innovations are welcome. It is a great way to unearth the impeccable source of new ideas.
Six Sigma is a powerful tool and is best implemented by Six Sigma-certified professionals who are trained in widely-recognized quality management certification courses. They are adept at using various tools and techniques to find the best solutions to eliminate such waste. However, the basic methodology is DMAIC, the set of 5 stage processes that helps you identify the waste. It also uses tools like value stream mapping, 5 WHY analysis, Just in time, and other tools to analyze and measure the problem.
Some of the popular quality management certification courses that individuals and enterprise teams can take up are: